کائولن چیست و بالکلی چیست، با معرفی کاربرد و آنالیز
کاربرد بالکلی، آنالیز بالکلی و بالکلی چیست، آنالیز کائولن، کاربرد کائولن، انواع کائولن کلوخه ، قیمت کائولن زنوز و خرید کائولن، قیمت خرید بالکلی
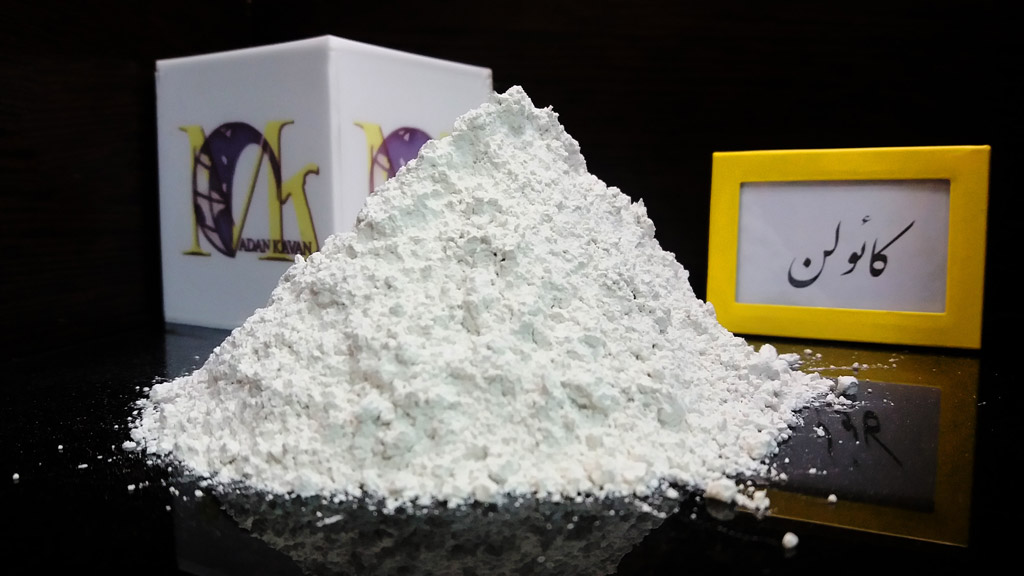
تاریخچه کائولن
واژه کائولن از سلسله جبال بلند کائولینگ به معنی قله مرتفع در ناحیه جیان کسی در کشور چین گرفته شده است که از خاک چینی سفید رنگ تشکیل شده است.
در اواسط دوران تانگ، قبل از میلاد مسیح، صنعتگران چینی قدم های نخستین را در تصفیه و پاک نمودن مواد اولیه جهت تولید کالاهایی برتر و عاری از نقص برداشته بودند. این تحولات ابتدا منجر به ساخت برخی ظروف سفالین با سنگنما به رنگ سفید شد که در تهیه آنها از خاک کائولن استفاده میگردید. آمیختن فلاسپات ها با کائولن منجر به تهیه ظروف مزبور گردید. که نوع بدنه آنها از استحکام، سفیدی متمایل به زرد و شفافیت متوسطی برخوردار بوده است.
بعلت استقبال فراوان از این ظروف، عرضه آنها در بازارهای جهانی افزایش پیدا کرد. اولین کارخانجات صنعتی ظروف پرسیلن یا چینی در چینگ ـ ته ـ چن تأسیس شد که صدها سال در این زمینه فعالیت میکردند. یکی از کشفیات قابل توجهی که در آن زمان حاصل گردید و بعدها مورد تقلید و دوباره سازی سایر صنعتگران قرار گرفت. استفاده از کبالت بخاطر رنگ آبی حاصل از آن در ترسیم نقوش بر روی ظروف مزبور بود. کبالت قبلاً بوسیله ایرانیان بر روی ظروف سفالین مورد استفاده قرار گرفته و از طریق آنها نیز به صنعتگران چین منتقل شده بود. بطور کلی تمام مراحل ساخت، اصول اولیه و فرمول چگونگی تهیه چینی آلات همیشه نزد چینیان مخفی نگهداشته میشد و آن ها همواره این اسرار را بصورت گنجی پاسداری میکردند.
کشور ژاپن را نیز از دیر زمان میتوان جزء یکی از اولین و بزرگترین تولید کنندگان کالاهای پرسیلن (چینیآلات) محسوب نمود. محصولات این کشور همیشه به تعداد فراوان و با مرغوبیتی متوسط در سطح جهان عرضه میشده است. فرآوردههای ژاپن اغلب از نقوش و فرمهای تقلیدی برخوردار بودند و گرچه از جهات تکنیکی در سطح عالی قرار داشتند ولی به لحاظ عدم ابتکار تولیدات نامحدود، محصولات چینی این کشور به لحاظ اهمیت در دوره دوم جهانی قرار دارد.
در چین سفرهای مارکوپلوو دیگران قطعاتی از چینیهای ساخت وارد اروپا گردید. در آن زمان اروپائیان ظروفی خشن و ابتدائی تولید میکردند که پس از مشاهده قطعات چینی کوشش فراوانی در ساختن ظروف چینی بکار بردند. صنعتگران اروپائی با اضافه کردن گرد شیشه به خاکهای سفید رنگ سعی نمودند که محصولات چینی مشابه محصولات کشور چین را تولید نمایند ولی این کشف تا سال ۱۷۰۹ که مقارن با شروع تحولات صنعتی در اروپا میباشد، بوقوع نپیوست.
در آن زمان یعنی اواخر قرن ۱۸ میلادی سفالگران با تجربه پی میبردند که تمام رازها در ترکیب کائولن، سیلیس و فلدسپات نهفته است و گفته میشود که این کشف برای اولین بار توسط بانگر که شاگرد یک دوافروش آلمانی بود انجام گرفته است، ولی امروزه این کشف را به گرافونت شرینهاس نسبت میدهند. در برخی نوشتهها به چگونگی روش ساخت چینی و ورود آن بصورت مخفیانه به اروپا توسط میسیونرهای مذهبی اروپائی اشاره شده است. این کشف به سرعت در تمام اروپا اشاعه پیدا کرد و کارخانجات چینی سازی در سرتاسر این قاره احداث گردید.
در انگلستان خاک سفیدی که از منطقه کورنوال استخراج میشود پرسیلن ادت به معنی خاک چینی مینامند. در طی سالهای اخیر همراه با گسترش دانش و کشف خواص گوناگون کائولن، این ماده جایگاه خاصی در صنعت کسب کرده و امروزه بعنوان ماده اولیه اصلی یا جنبی و کاتالیزور در بسیاری از صنایع استفاده میگردد.
کائولن در ایران نیز از دیر باز مورد توجه بوده و آثار حفریات قدیمی از قبیل تونل و گودالهای متعدد، حکایت بر شناخت آن نزد پیشینیان ایران زمین دارد. تاریخ معدنکاری بر روی کائولن در ایران به درستی معلوم نیست. در قرن نهم این اشیاء در بین ایرانیان بسیار رایج بوده و سفالگران سلاجقه و صفویه سعی فراوان در بازسازی آنها کردند. در عصر صفویان تعدادی از صنعتگران چینی نیز جهت تعلیم و آموزش به ایران آمدند ولی از این آموزش نتایج مطلوبی حاصل نشد. بجز آنکه ایرانیان بشدت تحت تأثیر نقوش و رنگهای هنرمندان چینی قرار گرفتند. از آن به بعد بتدریج پی به اهمیت و خواص کائولن بردند و در صنایع مختلف از آن استفاده کردند.
مشخصات کائولن ، آنالیز کائولن و کاربرد کائولن
کائولن یک اصطلاح اقتصادی است که برای کانسارهای رسی تقریباً سفید به کار می رود و از نظر صنعتی به رسی هایی که دارای مقدار قابل توجهی کائولینیت باشند،اطلاق میشود. این کانسارها اغلب شامل کانی کائولینیت و یا فرآورده های بدست آمده از آن می باشند. در گذشته اصطلاح خاک چینی به عنوان مترادف کائولن استفاده می شد. نام کائولن از کلمه کائولینگ چینی به معنای تپه سفید مشتق شده است که از آن خاک کائولن استخراج می شده است.
کائولن از مجموعه کانیهای رسی بوده و فرمول شیمیایی آن H۴Al۲Si۲O۹ می باشد.کانی های کائولن شامل کائولینیت، دیکیت، ناکریت و هالوزیت می باشد. فراوان ترین کانی این گروه کائولینیت می باشد. همه این کانی ها جزء کانی های آلومینو- سیلیکات می باشند که در سیستم مونوکلینیک و یا تری کلینیک متبلور می شوند. از مهم ترین خصوصیات کانی شناسی رس های کائولن نرمی و عدم سایندگی آنها می باشد. سختی کائولن در مقیاس موهر در حدود ۲-۵/۲ می باشد. این نرمی در کاربردهای صنعتی آن یک مزیت محسوب می شود.
رس های کائولن اکثراً از آلتراسیون کانی های آلومینیوم سیلیکات در نواحی گرم و مرطوب بوجود می آیند. فلدسپات ها از جمله کانی های عمومی منشاء پیدایش آنها می باشد. پلاژیوکلاز فلدسپارها (سدیم یا پتاسیم) معمولاً در ابتدا کائولینه می شوند. فلدسپارهای پتاسیک به کندی آلتره شده و تولید کائولن های مخلوط با سریسیت دانه ریز، ایلیت یا هیدروموسکویت می کند.
کائولن یا خاک چینی به رنگ سفید بیشترین کاربرد را در تولید چینی و سرامیک دارد.
به طور خلاصه خصوصیات مهم کائولن، که مصارف متعدد آن را سبب شده است می توان به صورت زیر نام برد:
- از نظر شیمیایی در گستره وسیعی از تغییرات PH بدون تغییر می ماند.
- داشتن رنگ سفید که آن را به صورت ماده رنگی قابل استفاده می سازد.
- دارا بودن خاصیت پوششی بسیار خوب
- نرمی و غیر سایشی بودن آن
- قابلیت اندک هدایت جریان الکتریسیته و گرما
- قیمت ارزان
کائولن از نظر صنعتی به رسهایی که دارای مقدار قابل توجهی کائولینیت باشند اطلاق میگردد. کائولینیت، یک کانی رسی صفحه ای به رنگ های سفید (در حالت خالص) و خاکستری متمایل به زرد بصورت خاک رس بسیار نرم و ظریفی است که در اثر فشردن بین انگشتان خرد شده و پودر میگردد. سختی آن یک (در مقیاس موس) و در حالت متبلور به ۵/۲- ۲ میرسد. وزن مخصوص آن ۳gr/cm2.6 و نقطه ذوب ۱۷۸۵ درجه سانتی گراد میباشد.
کائولن از نظر کانی شناسی جزء گروه کانی های سیلیکات آلومینیوم آبدار است. فرمول عمومی کائولن H۴Al۲Si۲O۹ میباشد که دارای ۵/۳۹درصدAl۲O۳ 3،/۴۶درصدSiO۲و۱۴درصد آب است.
این کانی به سهولت در آب و عموماً در مایعات پراکنده میشود، نفود ناپذیر بوده و در حالت خشک مقدار زیادی آب از دست می دهد اما منبسط نمیگردد. همین خاصیت کائولن را از گروه اسمکتیت متمایز مینماید. خمیر آن با آب، شکل پذیر بوده و با پختن، شکل و رنگ آن تغییر نمی کند. در اثر دمیدن بر روی آن بوی خاک میدهد. شکستگی و کلیواژ آن قاعدهای کامل دارد و جلای آن تیره (خاکی) تا مرواریدی تیره میباشد. دارای لمس چوب و صابونی است و مزه خاک رسی دارد. قابلیت هدایت جریان الکتریسته و گرمای آن اندک است. انقباض طولی آن در ۱۳۰۰ درجه سانتیگراد از ۶ درصد تا ۱۷ درصد متغیر میباشد و در شیشهسازی این مقدار حتی به ۲۰ درصد هم میرسد. هنگام پخت به شدت منقبض میشود و رفتار آن در برابر دما عموماً مرتبط به آب موجود در آن، خصوصاً آب بشکهای، بسیار قابل توجه است. بی آب شدن کانههای رسی از جمله کائولینیت عموماً در برابر دما، دگرگونی هایی را در ساختمان این کانه پدید میآورد.
چسبندگی یکی دیگر از خواص مهم فیزیکی کائولن است زیرا این ویژگی با درجه خلوص آن نسبت مستقیم دارد، یعنی هرچه درجه و میزان چسبندگی در کائولن بیشتر باشد به همان نسبت درجه خلوص کائولن نیز افزایش مییابد. کائولن مرغوب کائولنی است که اگر یک تکه از آن را به زبان بزنیم روی زبان بچسبد و این خود یکی از بهترین و سادهترین روشهای تشخیص کائولن است. کائولن از نظرکانی شناسی جزء کانی های سیلیکاته آلومینیوم آبدار است.
کانیهای این گروه عبارتند از : کائولینیت، دیکیت، ناکریت و هالوزیت و همچنین متاهالویزیت و خاک نسوز میباشد.
از جمله خصوصیات اقتصادی مهم کائولن اندازه ریز ذرات آن می باشد. اغلب دیگر موادی که به عنوان رنگدانه، پرکننده، پوشش دهنده و روان ساز استفاده می شوند، باید به وسیله عملیات هزینه بر خردایش و آسیا کردن، کاهش اندازه داده و به پودر تبدیل شوند. علاوه بر هزینه بری، تقلیل اندازه آنها نیز تصادفی بوده و به طور غیرمنظم شکسته می شوند. کائولن از مجموعه های سستی از بلورهای ریز که بیشتر شکل و اندازه ثابتی دارند، تشکیل شده است و نیز اندازه مورد استفاده در صنعت کمتر از دو میکرون بوده و این یک مزیت اقتصادی برای آن محسوب می شود. بنابراین در صنعت نیز اندازه ذرات کائولن را بر حسب درصد وزنی ذرات کوچک تر از دو میکرون بیان می کند.
از خصوصیات شیمیائی دیگر کائولینیت آن است که در گستره وسیعی از تغییرات PH تغییر نمیکند ولی در اسید سولفوریک غلیظ حل شده، ژل سیلیسی از خود بجا میگذارد. گداخته آن در اسید کلریدریک نیز حل میشود.
یکی از مهم ترین خصوصیات صنعتی کائولن ماهیت شیمیایی خنثی آن می باشد. کائولن تحت شرایط شیمیایی صنعتی و در محدوده PH بین ۳ تا ۹ پایدار می باشد. بنابراین می تواند به راحتی به عنوان رنگدانه، پوشش و پرکننده با سایر ترکیبات استفاده شود.
کائولینیت در دمای ۳۰۰-۲۵۳ درجه سانتیگراد بخش زیادی از آب خود را از دست میدهد و در دمای ۶۵۰ درجه سانتیگراد تمامی ملکولهای آب موجود در شبکه ساختمانی آن بخار میشود. در دمای ۸۰۰ درجه سانتیگراد این عمل پایان مییابد و یک کانی به شکل نیمه بلورین بنام متاکائولن پدید میآید. مجموعه واکنش های فوق تا پایان این مرحله از نوع حرارتگیر است. چنانچه دما از ۸۰۰ درجه سانتیگراد بالاتر رود، ساختمان لایهای کانه شکسته شد و دیگر توان جذب آب دوباره را ندارد. در دمای ۹۲۵ درجه سانتیگراد واکنش حرارت زایی آن آغاز میشود و در این مرحله با خارج شدن سیلیس از متاکائولینیت مازاد، ترکیب بصورت یک فاز شبکه اسپینل (۲SiO3 ,۳O۲Al2) درمیآید. سیلیس آزاد شده بصورت بیشکل (آمورف) و یا نیمه بلورین پدیدار میشود. به گونهای که شناسایی آن با آزمایش دیفراکسیون اشعه ایکس امکانپذیر نمیباشد. در دمای حدود ۱۱۰۰-۹۵۰ درجه سانتیگراد این فاز شبه اسپینل شروع به شکسته شدن کرده و بخش زیادتری از سیلیس خود را آزاد میکند.
فرآورده پایانی این مرحله مولیتی است که احتمالاً مقدار سیلیسی آن از ترکیب طبیعی مولیت بیشتر و سیلیس پدید آمده بصورت کریستوبالیت میباشد که امکان شناسائی آن با اشعه ایکس وجود دارد.
کانیهای بدست آمده بصورت کریستوبالیت میباشد که امکان شناسائی آن با اشعه ایکس وجود دارد.
کانیهای بدست آمده از واکنشهای یاد شده با بالا رفتن دما ناپایدار میشوند و در این راستا همواره بسوی نوعی ناپایداری بیشتر میروند. از این رو در دماهای بالاتر از ۱۳۰۰ درجه سانتیگراد یا بیشتر از این مسیر تعادلی کانیهای کامل شده و به مرحله پایداری میرسند. در این مرحلکه کانی مولیت بدون سیلیس مازاد پدید میآید. بنابر این فاز پایانی این فرآیندهای حرارتی شیمیایی، مولیت و کریستوبالیت میباشد که مقدار کمی کوارتز و بندرت تریدیمیت آنها را همراهی میکنند.
سنگ کائولین برحسب نوع پیوندهایش به دو گروه پیوند نرم و سخت تقسیم میشوند:
۱- کائولن دارای پیوندهای نرم که عمدتاً در صنایع کاشیسازی و چینیسازی و سرامیکسازی و مجمسهسازی مورد استفاده قرار میگیرند. پیوند در این کائولن فقط با هیدرات میسر است.
۲- کائولن دارای پیوندهای سخت که عمدتاً در صنایع لاستیکسازی و کاغذسازی مصرف دارند. پیوند در این نوع فقط با کلسیم امکانپذیر است و اصطلاحاً در چنین حالتی شبکه پر میباشد.
روش های اکتشاف کائولن
اکتشاف کائولن همانند اکتشاف هرکانسار غیرفلزی دیگر، شامل سه مرحله نمونهبرداری، تجزیه و اندازهگیری کمیتهای موردنیاز و بالاخره تحلیل دادهها، بخصوص مطالعه تغییرپذیری کمیتهای موردنیاز درکل نهشته (کانسار) میباشد. سپس با حذف مناطقی که کیفیت مناسب را دارا نمیباشند، باید به محاسبه و تعیین ذخیره و نهایتاً رسم منحنیهای عیار ذخیره پرداخت. دراینجا بحث عیار کمی پیچیدهتر از عیار درکانسارهای فلزی است، زیرا درکانسارهای غیرفلزی، بخصوص در کانههای رسی، ترکیب شیمیایی و خواصی که میتواند مفید یا مضر باشند از پیچیدگی بیشتری برخوردار هستند، بنابراین منظور از عیار در اینجا حدود قابل قبول خواص کائولن میباشد. حال در ذیل به هریک از مراحل فوقالذکر میپردازیم:
۱) نمونهبرداری
شکی نیست که به منظور طراحی بهینه نمونهبرداری از یک کانسار کائولن، میبایستی قبلاً اطلاعاتی درمورد موقعیت کانسار بدست آورد و به درک صحیحی از موقعیت زمینشناسی آن دست یافت. بنابراین بخش بزرگی ژنز کانسار ضروری است. این امر از آن جهت با اهمیت است که میتواند ما را در شناخت تغییرپذیرهای اولیه و کمیتهای مهم یاری دهد. برای مثال دریک کانسار کائولن هیدروترمال (هیپوژن) که شدت فرآیند کائولینیتیزاسیون بشدت تابع عمق است، ممکن است مقدار سیلیس اضافی که همراه این نوع کانسارها دیده میشود، در زون سلیسیفیکاسیون، بشدت افزایش یابد. درهمین تیپ کانسارها، ممکن است بعلت تغییرپذیری شدت لیچینگ، مقدار عناصر قلیایی و قلیایی خاکی دربخشی از کانسار از مرغوبیت و کیفیت مطلوب برخوردار نباشد، و یا زونهای پیریتی که ممکن است با این تیپ کانسارها همراه نباشند، پس از اکسیداسیون موجب افزایش مقدار کانیهای آهندار شده و از مرغوبیت بخشی از کانسار بکاهد.
همچنین موقعیت فضائی کانسار (توسعه ابعاد کانسار در سه جهت) نیز از اهمیت خاصی برخوردار است، زیرا در کانسارهای هیدروترمال با شیب تند، اغلب متغییرهای فوق در امتداد قائم منطقهبندی میشوند، درصورتی که در کانسارهای با شیب ملایم از این نوع، همین تغییرات، ممکن است با شیب ملایم نسبت به عمق دیده شود ولی تغییرات جانبی در تعداد شمالی- جنوبی و یا خاوری- باختری ممکن است بیشتر باشد.
درمورد کانسارهای برجای کائولن، درک صحیحی از پالئوژئوگرافی نیز میتواند درمحلی با انباشتگی زیاد و یا کم در اکتشاف کمک نماید و درمورد کانسارهای رسوبی که فاز حمل و نقل را نیز تحمل نمودهاند، جهت جریان آبهای سطحی درجهت کشف بخشهای ضخیم نیز میتواند مفید واقع گردد. اطلاعات زیر در شناخت ژنز کانسار بسیار مهم بشمار میروند.
مشخصات سنگشناسی، کانیشناسی و همچنین وضع ریزشهای جوی و توپوگرافی ناحیه منشاء که با مستقیماً از طریق هوازدگی باعث تولید کانیهای رسی از جمله کائولن گردیده و یا برای مثال تولید ماسه سنگ فلدسپاتی را سبب شده که خود میتواند در تحولات بعدی به کائولن تبدیل شود.
وضع تکتونیکی ناحیه منشاء، که خود بشدت روی سطوح پالئوتوپوگرافی اثر داشته و آن را کنترل مینماید. علاوه برآن عوامل تکتونیکی میتواند در تغییر دادن نسبت تخریب شیمیایی (تولید کائولن در ناحیه منشاء) به تخریب مکانیکی (تولید ماسه سنگ فلدسپاتی یا میکایی) مؤثر واقع گردد. درحالتی که نسبت تخریب مکانیکی به شیمیایی بالا باشد، ماسه سنگ فلدسپاتی پس از حمل و نقل و رسوبگذاری در محیط رسوبی، شانس تبدیل شدن به موادرسی از جمله کائولن را دارا میباشد.
مورفولوژی حوضههای رسوبی و همچنین توزیع انرژی در آنها نیز از اهمیت خاصی برخوردار است، زیرا در حوضههای رسوبی پرانرژی، مخلوط ماسه و رس کائولنی شانس بسیار زیادی برای جداکردن ایندو از یکدیگر داشته و درنتیجه باعث بالا رفتن عیار کائولن رسوبی خواهد شد.
الف ـ طراحی نمونهبرداری سطحی
به منظور طراحی نمونهبرداری سطحی، لازم است تا اطلاعاتی که در فوق به آنها اشاره شد. در مورد ژنز کانسار، در اختیار قرار بگیرد و سپس براساس تغییرات لایهبندی و شناخت امتداد و حداکثر و حداقل تغییرپذیریهای سطحی ممکن، اقدام به برداشت تعدادی نمونه در امتداد پروفیل که امکان تغییرپذیری بر روی آنها حداکثر است نمود. سپس براساس اطلاعات حاصل از آنالیز نمونهها، در صورت نیاز به برداشت نمونه سطحی بیشتر اقدام نمود.
ب ـ نمونهگیری عمقی
جهت نمونهگیری عمقی، اقدام به حفاری مغزهگیری با استفاده از شبکههای حفاری میگردد برای حفاری با قطر زیاد موردنظر هستند، استفاده از گل حفاری بنتونیتی بدلیل امکان آلودگی ماده معدنی در حفاری کائولن محدود گردیده است. تعیین مناسبترین مکانهای حفاری اوگری یا مغزهای براساس اطلاعات بدست آمده از مطالعات سطحی امکانپذیر میباشد.
۲) تعیین تستهای لازم
تعیین تستهای لازم جهت اندازهگیری خواص مهم و ویژهای که برحسب مورد مصرف تکنولوژیکی ماده معدنی تغییر خواهدکرد. بسیار با اهمیت است. دراین خصوص لیستی از متغیرهای مختلف در ذیل ذکر شده است، ولی لازم به توضیح است که در همه موارد نیازی به اندازهگیری همه این متغیرهای نخواهد بود. بلکه از بین آنها میتوان با توجه به اهداف مصرفی ماده معدنی، تعدادی از آنها را که در ارزیابی ماده معدنی مفید واقع میشوند، انتخاب نمود.
الف ـ تعیین ترکیب شیمیایی:
شامل اکسیدهای اصلی: MgO_ CaO-FeO-Al۲O۳-SiO۲-Na۲O-K۲O
تعیین عناصر کمیاب نظیر: ارسنیک، آنتیموان، جیوه، بر
ب ـ تعیین ترکیب کانیشناسی:
از آنجا که ممکن است کائولن همراه کانیهای رسی دیگر از خانواده اسمکیت (مونت موریونیت)، الیت، سریسیت باشد درنتیجه شناخت آنها ضروری است.
ج ـ تعیین دانهبندی
درمورد کائولنهای نرم که معمولاً در کانسارهای رسوبی توسعه یافته، در آبهای شیرین تشکیل میشوند، ماکروکریستالهای کائولینیت، دانه درشتترند، درصورتی که کائولنهائی که در حوضههای رسوبی آب شور تشکیل میشوند، معمولاً دانه ریزترند.
د ـ درجه سفیدی
این عامل تا حدودی تابع مقدار آهن و سایر اکسیدها و هیدروکسیدهای فلزی است.
ه ـ تعیین قدرت جذب و تعادل یونی
و ـ تعیین نقطه ذوب
ز ـ تعیین نقطه شیشهای شدن
ح ـ تعیین وزن مخصوص
ت ـ تعیین وزن نسوزندگی
ی ـ تعیین رنگ پس از پخت
محاسبات آماری و تخمین تغییرپذیری خواص اندازهگیری شده
تعیین عیار
پس از بررسیهای سطحی و آنالیز نمونههای عمقی، عیار ماده معدنی (ماده معدنی با کیفیت مناسب) و همچنین ضخامتی که در آن، عیار ثابت درنظر گرفته میشود. مشخص میگردد و سپس کل کانسار به بلوکهای متفاوتی از نظر کیفیت تقسیم میشود.
تهیه نقشههای موردنیاز زمینشناسی و توپوگرافی (محاسبه ذخیره هر بلوک که در سراسر آن خواص مفید یا مضر ماده معدنی ثابت فرض میشود).
رسم منحنیهای کیفیت ذخیره براساس اطلاعات بدست آمده از کلیه بلوکها
ارزیابی اقتصادی کانسار
در ارزیابی یک ذخیره کائولن، پارامترهای تجاری مهم بوده، و درتمام مراحل اکتشاف باید مورد توجه قرار بگیرد. از جمله شفافیت، رنگ پخت، سفیدی، قطر اجزاء، خواص شکلپذیری و خواص حرارتی.
کاربرد روش ژئوفیزیکی در شناسایی زون های کائولن
یکی از روش های متداول و مؤثر در شناسایی و تعیین زون های غنی از کائولن استفاده از روشهای ژئوفیزیکی میباشد.
در اکتشاف کائولن چنانچه تمایز خاک چینی و سنگهای دربرگیرنده قانع کننده نباشد، روشهای ژئوفیزیکی میتواند جهت تشخیص و تعیین کانسار و کاهش هزینههای حفاری مورد استفاده قرار بگیرد.
برای این کار ابتدا برداشت پروفیل ژئوفیزیکی با روش IP و سپس مطالعه دقیق کانیشناختی و سنگ شناختی، برای تفکیک زونهای آلتره و تهیه نقشه دقیق گسترش ماده معدنی انجام میگیرد. در مرحله بعد درصورت مثبت بودن شواهد و دلایل کانیسازی، مطالعه ژئوفیزیکی دقیق با روشهای الکتریکی انجام میپذیرد.
کاربرد دادههای ماهوارهای و ژئوفیزی هوایی در اکتشاف کائولن
عکسبرداری هوایی و استفاده از عکسهای هوایی در بررسیهای زمینشناسی سابقه طولانی دارد. در تکامل بررسی فوق، مطالعه منابع معدنی با استفاده از سنجش از دور ماهوارهای پا بر عرضه گذاشته است. استفاده از مشخصههایی که مواد معدنی و کانسارهای مختلف در نگارههای هوایی نشان میدهد، به تحلیل و ارزیابی کانسار و سنگهای میزبان کمک مینماید. تغییرات رنگی تابع عوامل مختلف نظیر هوازدگی سنگ بستر، پوشش گیاهی و سایر عوارض طبیعی زمین است. اساس کار بدین صورت است که امواج الکترومغناطیس منعکس شده از اشیاء توسط دستگاههای حساس که در داخل ماهواره جای گرفتهاند مثبت شده و بصورت نوار یا فیلم به زمین مخابره میشود.
اصولاً اکتشاف هر ماده معدنی، شامل دوقسمت میباشد. در این قسمت به نحوه اکتشاف در یک منطقه معدنی پرداخته میشود، یا بعبارت دیگر چه مراحلی باید طی شود تا یک معدن بطور دقیق و علمی شناسایی و تعیین ذخیره گردد.
پس از بررسیهای نقشههای زمینشناسی با مقیاس کوچک، مناطق موردنظر تعیین و برای پیجویی مقدماتی اکیپهای پیجویی شروع بکار مینماید.
اکیپهای پیجویی که در واقع یا بندگان معدن میباشند با استفاده از نقشههای توپوگرافی و جغرافیا و همچنین عکسهای هوایی شروع به تجسس مینمایند و پس از بررسی کامل منطقه از نظر زمینشناسی، چینهشناسی، رسوبگذاری، تکتونیک، برداشت نمونه از لایههای حاوی ماده معدنی اقدام به تهیه گزارش نموده و درصورتی که نتایج مطالعه صحرائی و نتایج آزمایشگاهی مثبت باشد منطقه قابل کار تشخیص داده میشود. در این حالت ممکن است نقشههای کوچک مقیاس نیز تهیه گردد و بدین ترتیب کار گروه پیجوئی خاتمه مییابد.
گروه اکتشافی از این مرحله به بعد وارد عمل میشود. هرگروه اکتشافی متشکل از قسمتهای زمینشناسی، حفاری و نقشهبرداری است که زیرنظر سرپرست گروه کار میکنند.
روشهای عمده استخراج کائولن
به روشهای مختلف روباز استخراج میشود. انواع بیلها، کجبیلها، اسکراپر و… در استخراج کائولن بکار میرود. همچنین استخراج بوسیله لدرهای هیدرولیکی یا شیارکشها صورت گرفته و انتقال آن به محل کارخانه با کامیون، تسمهنقاله، خطوط لوله و… انجام میپذیرد.
کائولنهای نرم و شکننده با فشار آب که از دور توسط مونیتور کنترل میشود، برداشت میشود. معدنکاری بهصورت انتخابی براساس دادههای حفاری صورت میگیرد.
استخراج کائولن در دنیا عمدتاً بصورت روباز صورت میپذیرد. هر چند در استخراج این ماده معدنی، ماشینآلات و تجهیزات خاصی موردنیاز نمیباشد. اما وجود ماشین آلاتی از قبیل لودر، بولدوزر، کامیون، تانکر، پیکور، دیزل ژنراتور … با تعداد متفاوت برحسب ظرفیت استخراج اجتنابناپذیر است. از آنجائی که باید سعی شود که دربرداشت ماده معدنی، ناخالصیها و کانیهای همراه کائولن به میزان حداقل ممکن باشد. لذا استخراج آن باید دقت کافی صورت پذیرد.
به منظور انتخاب یک روش استخراج مناسب باید اطلاعات زمینشناسی کانسار از قبیل وضعیت توده معدنی، شکل، شیب،
اندازه، عیار و توزیع کانی مورد توجه قرار گیرند. همچنین دادههای زمینشناسی و معدنی کانسار از قبیل وضعیت سنگ معدنی و سنگهای درونگیر، گسلها، درزهها و عوامل تکتونیکی و نیز آبهای سطحی و فشارهای طبقات مدنظر قرار داده شوند.
روش های متداول فرآوری کائولن
کائولن ابتدا بهصورت خشک فرآوری میشود که شامل خردکن، خشککردن و نرمکردن است، که محصول آن کائولن با کاربری در سرامیک، رنگ و لاستیک است. فرآوری تر، یا شستشو با آب کانیهای غیرکائولن را از مایع رسدار جدا میکند، که در این مرحله کائولن با کاربری به عنوان پرکننده و پوشش حاصل میشود. در انواع سرندها، هیدروسیکلونها و… مایع رسی را میتوان تا حد ۳۰% جامد در مخزن تهنشینی غلیظ کرد و با سانتریفوژ کردن، ۷۵% ذرات با اندازه ۲ میکرومتری را از آن جدا کرد، ذرات درشت با اولترافلوتاسیون ریزشده و بعد مراحل تورق زدایی، غربال کردن، فیلترکردن و خشک کردن و گاهی تکلیس برروی آن انجام میشود.
در حالت دیگر مایع کائولندار به دو دسته ریز و درشت با استفاده از سانتریفوژ، هیدروسیکلون یا جداسازی با آب بطور ممتد تقسیم شده و بعد ترکیبات آهندار رنگزا از آن شسته می شود. بعد از آبگیری با تبخیر، فیلتر مکش چرخان یا فشاری، کیک کائولنی را میتوان خارج کرد و خشک نمود و یا به صورت ماده با ۷۰% جامد برای دادوستد منتقل کرد.
درتورقزدایی، ذرات کائولن به صورت مکانیکی به ذرات روشن و نازکی جدا شده و در دما C °۵۰۰ تکلیس میشوند تا ساختار بلوری مجزایی در آن بوجود آید. این عمل سبب افزایش درخشندگی و کدری کائولن می شود.
حتی بهترین کائولن های دنیا هم در حدود ۲۰ % ناخالصی دارند. بنابراین بایستی آنها را تغلیظ کرد و مواد قلیایی آن را به کمتر از ۵/۱ % رساند.
کائولن مصرفی باید دارای مشخصات ذیل باشد :
۱-درصد Al۲O۳ باید از ۳۰ % بیشتر باشد.
۲-میزان اکسیدهای آهنFe۲O۳ نباید از ۱ درصد بیشتر شود.
۳-میزان اکسید تیتانیوم TiO۲ باید به ۲/۰ درصد کاهش یابد.
۴-اکسیدهای قلیایی نباید از ۲ درصد بیشتر شود.
۵-حداکثر میزان CaO، ۲/۰ درصد و MgO، ۳/۰ درصد باشد.
۶-افزایش میزان کائولینیت نسبت به سایر کانی های موجود باعث مرغوبیت کائولن می شود.
۷-دیر گدازی کائولن باید در حدود ۱۷۰۰ درجه سانتیگراد باشد.
۸-مدول گسیختگی آن باید بیش از ۱۰ کیلوگرم بر سانتی متر مربع باشد.
هدف از آرایش کائولن جدا کردن ناخالصیهای موجود در آن است. به طور کلی عمل جدا کردن ناخالصیهایی نظیر زاج، گچ، پیریت و فلدسپاتها تجزیه نشده از کائولن را کانهآرایی کائولن میگویند و اصطلاحاً به عمل جدا کردن عناصر مزاحم نظیر سدیم، پتاسیم و کلسیم توسط آب، کائولنشویی گفته میشود.
مبنای آرایش کائولن در بیشتر موارد طبقه بندی آن از نظر ابعاد است، زیرا با توجه به قابلیت خرد شدن بیشتر کائولن نسبت به ناخالصیهای همراه آن مثل کوارتز، میکا و همچنین توجه به این نکته که کائولن دارای خاصیت جذب آب شدیدی میباشد و در وقت کم بصورت خمیری با شکلپذیری زیاد و نیز در وقت زیاد بصورت ذرات دانه ریز در آب معلق میشود، میتوان آن را از ناخالصی های همراه جدا کرد. مراحل آرایش کائولن بسته به کیفیت ماده معدنی و مشخصات مورد نظر در محصول آراسته ممکن است بسیار ساده یا پیچیده باشد. در بسیاری از موارد بافت کانسنگ به نحوی است که در تماس با آب در ابعاد طبیعی یا پس از خرد شدن تنها در مرحله سنگشکنی، ذرات کائولن از ناخالصی های همراه جدا شده بصورت دانه ریز در محیط پراکنده میشوند. بالطبع آرایش این نوع مواد سادهتر است، زیرا ناخالصی های همراه کائولن بصورت ذرات دانه درشت وجود دارند. برعکس در بعضی موارد دیگر، بافت ماده اولیه کائولن بسیار دانه ریز و متراکم است و تنها در تماس با آب ذرات کائولن نمیتوانند از ناخالصی ها جدا شوند در این موارد گاهی لازم است که ماده معدنی تا ابعاد دانه ریزتری آسیا شود.
آسیا کردن ماده معدنی از یک طرف هزینه عملیات را بشدت افزایش میدهد و از طرف دیگر باعث خرد شدن بخشی از ناخالصی ها تا ابعاد میکرونی میشود. در نتیجه این قبیل ناخالصی ها نیز همراه محصول آراسته کائولن باقی مانده و کیفیت آن را کاهش خواهند داد.
ذکر این نکته ضروریست که در بسیاری از موارد ساختار کانسار وضیعت لایهها و رگهها به نحوی است که امکان استخراج انتخابی کائولن برای رسیدن به کیفیت بهتر وجود دارد، برای این منظور لازم است از کانسار بطور منظم نمونه برداری شود و مورد آزمایش قرار گیرد و بر مبنای نتایج حاصله روش استخراج انتخاب شود.
امروزه پیشرفت های زیادی که در زمینه فرآوری کائولن صرت گرفته، که به اقتضای خواص مورد نظر صنایع مصرف کننده بوده است. بخصوص صنعت کاغذسازی که مصرف کننده عمده کائولن بعنوان پوشش دهنده میباشد.
پیشرفت های ویژه در این زمینه عبارتند از:
۱-استفاده از سانتریفوژ پیوسته جهت طبقهبندی مواد از ابعاد میکرونی
۲-کاربرد همزههای قوی و بزرگ جهت تفرق کائولن در کارگاه مستقر در معدن
۳-حمل و نقل کائولن بصورت پالپ
۴-جایگزینی فیلتر پرسهای صفحهای و قابی با صافیهای خلاءاستوانهای،دوار و پیوسته.
۵-بکارگیری خشک کنهای افشانگی
۶-نصب تکلیش کنندهها جهت تولید رنگدانه با درخشندگی زیاد
۷-گسترش تکنیکهای فلوتاسیون جهت حذف ناخالصیهای بسیار ریز آهن و تیتانیم.
۸-توسعه تکنیک های متورق سازی که صفحات انباشته شده ذرات را به صفحات مجزا و بزرگ با خواص پر کنندگی و پوششی خوب جدا کنند.
۹- توسعه جدا کنندههای مغناطیسی با شدت زیاد.
روش فرآوری سنگ معدنی کائولن به نوع مصرف محصول بستگی دارد اساساً دو فرآیند کلی متفاوت در صنایع تولید کائولن بکار میرود،فرآیند خشک و فرآیند تر.
الف) روش خشک
هر چند امروزه در اکثر معادن،روشه ای خشک بعلت بازدهی و دقت کمتر به تدریج جای خود را به روش های تر دادهاند. با این وصف ممکن است بعلت کیفیت ماده اولیه، استفاده از روش های خشک امکانپذیر باشد و با کمبود آب در ناحیه معدنی و یا هزینه زیاد تهیه آب مورد نیاز، استفاده از روش های خشک را ضروری میسازد.
در صورت استفاده از روش های خشک رطوبت ماده اولیه بایستی کمتر از ۱ تا ۲ درصد باشد و در صورتی که بیشتر از این مقدار باشد خشک کردن آن در کوره (معمولاً کورههای دوار) الزامیست. عملیات خشک کردن را می توان در حین آسیا کردن مواد، با دمیدن هوای گرم به داخل آسیا انجام داد. تلاطم هوا و ذرات در داخل آسیا و توجه به این نکته که قسمت های سطحی قطعات ماده اولیه بلافاصله پس از خشک شدن بصورت ذرات ریز در هوا متفرق میشوند، باعث میشود که قسمت های میانی قطعات در تماس با هوای گرم قرار گیرد و با ایجاد سیستم تبادل حرارت بسیار خوب در محیط، عملیات خشک کردن تقریباًفوری انجام گیرد. خرد کردن کائولن به روش خشک را میتوان با آسیاهای گلولهای، چکشی و غلطکی انجام داد. طبقهبندی مواد خرد شده توسط کلاسیفایرهای هوایی انجام میشود.
کلاسیفایر مناسب برای کائولن با ترکیبی از جریان هوای رو به بالا و نیروی گریز از مرکز کار میکند و از دو مخروط، که یکی در داخل دیگری قرار گرفته است تشکیل شده است. جریان هوا بین این دو مخروط داخلی را یک و نتیلاتو تامین میکند. برای آنکه هوا بتواند در مسیری بسته جریان داشته باشد، برشی در جداره مخروط داخلی ایجاد شده است. مواد اولیه از طریق یک محور تونلی وارد کلاسیفایر میشود و به توسط یک صفحه گردان در داخل کلاسیفایر توزیع میشوند. اولین طبقهبندی در اثر جریان هوای رو به بالا و طبقهبندی دوم توسط پرههای چرخان که در بالای کلاسیفایر نصب شدهاند انجام میشود. ذرات دانه درشت در اثر نیروی گریز از مرکز به بدنه مخروطی داخلی بر میخورد و در امتداد آن به طرف پایین حرکت میکند و از دهانه مخروط خارج میشود مخروط خارجی نقش یک سیکلون گردگیر را ایفا میکند. ذرات کائولن در امتداد جدار مخروط خارجی به طرف پایین حرکت میکنند و هوای تمیز شده از طریق برش مخروط میانی به مسیر برگردانده میشود. حد جدایش این وسیله را میتوان با تنظیم تعداد تیغههای و انتیلاتور و چرخان و سرعت گردش آن کنترل کرد.
محصول این روش عموماً بعنوان پر کنندههای ارزان در لاسیتک، پلاستیک و صنعت کاغذ (در جایگاه درخشندگی حساسیت زیادی ندارد) استفاده میشود.
ب) روش تر
در این روش کائولن با افزودن مواد شیمیایی متفرق سازی در یک همزن بالنجر به صورت یک پالپ در میآید. آنگاه پالپ مزبور توسط کلاسیفایرهای جامی یا سیکلونها از شن و ماسه عاری شده و سپس به دو بخش دانه درشت و دانه ریز با استفاده از سانتریفوژهای پیوسته، هیدروسیکلون ها، جداکنندههای آبی یا سرندهای لرزان طبقه بندی میگردد.
بخش دانه ریز از این کلاسیفایرها در معرض جدا کنندههای مغناطیسی با شدت زیاد جهت حذف اولیه آناتاز قرار داده میشود. و نیز بار حذف اکسید آهن مورد فروشوئی قرار میگیرد. اما وقتی یک رس درخشندگی کافی و خصوصیات پوششی خوبی دارد، میتواند مستقیماً به مرحله فروشوئی وارد شود، بدون اینکه تحت فرآیند جدایش مغناطیسی و یا متورق سازی قرار گیرد.
فرآیند فروشوئی با استفاده از محلول اسید سولفوریکو در حضور یک عامل احیا کننده نظیر هیدروسولفیت سدیم یا روی جهت حفظ انحلال آهن و جلوگیری از تشکیل هیدروکسید آهن سه ظرفیتی انجام میشود. زاج نیز جهت لخته شده رس به آن اضافه میشود تا به آبکشی کمک کند رس شسته شده با استفاده از سانتریفوژ با سرعت زیاد،صافی های خلاء دوار یا فیلتر پرس آبکشی میشود.
بدون استفاده از جدا کننده مغناطیسی محصول نهایی میتوان درخشندگی در حدود ۸۵-۷۵ ISO داشته باشد. رس هائی با درخشندگی بالای 90ISO از تلفیق جدا کننده مغناطیسی و فلوتاسیونو یا فلوکولاسیون انتخابی در خط تولید بدست میآیند. هر یک از این روش ها مزایا و محدودیت های خاص خود را دارند و بنابراین ترکیبی از دو یا سه روش فوق در صنعت جهت رسیدن به بهترین کائولن از ماده خام متداول است.
روش های زیادی برای فرآوری کائولن در دنیا به کار میرود. یکی از روشهای قدیمی روش سنگ جوری دستی است که شامل انتخاب و جدا کردن قطعات نسبتاًدرشت ناخالصی های کائولن (در حد بزرگتر از چند سانتیمتر) روی نوار نقاله توسط تعدادی کارگر است.
با توجه به قابلیت خرد شدن بیشتر کائولن نسبت به اکثر ناخالصی های همراه آن، درصورتی که ابعاد ناخالصی ها پس از آزاد شدن کائولن بزرگتر از چند میلیمتر باشد، میتوان آن ها را توسط سرند از ناخالصی ها جدا کرد. سرند کردن ممکن است به طریقه خشک یا تر انجام شود.
روش کانال های طویل،روش قدیمی است که در آن از کانال طویلی با شیب کم استفاده میشود که در مسیر آن حفرههائی پیشبینی شده است. ناخالصیهای موجود در کائولن با توجه به ابعاد بزرگتری که دارند و همچنین ناخالصیهایی که دارای جرم مخصوص بیشتری هستند عمدتاًدر داخل حفرهها سقوط میکنند. کائولن آراسته پس از عبور از کانال خارج میشود. اشکال این روش طولانی بودن مسیر و زمان بیشتر مورد نیاز برای آرایش و همچنین احتیاج داشتن به تعداد زیادی کارگر است.
۲) فیلتراسیون
در این مرحله آبگیر، تجهیزات اصلی مورد استفاده عبارتند از: فیلت پرس ها، سانتریفوژهای با سرعت زیاد، فیلترها خلاء گردان و فیلترهای لولهای، فیلتر پرس های صفحهای پالپی را که درصد جامد کمی دارد، با اعمال فشار تغلیظ کرده به حدود ۷۰% جامد میرسانند. این عمل در فشاری درحدود ۸ تا ۹ باز انجام میشود. کیک فشرده شده در حالیکه هنوز بخاطر رطوبت خود چسبنده است باید بطور دستی از دستگاه پرس تخلیه شود.
با استفاده از فیلت استوانهای گردان غلظت پالپ به ۶۵-۵۵ درصد جامد افزایش مییابد. یک فیلتر بزرگ (با حدود ۴ متر قطر و ۱۱ متر طول) میتواند ۱۲ تا ۱۵ تن بر سرعت رس از درجه پوشش و ۳۰ تن بر ساعت رس از درجه پر کننده تولید کند. یکی از وظایف مهم فرآیند فیلتراسیون حذف مواد شیمیایی از رس است. جهت تسهیل در این کار از دوش آب استفاده میشود.
قابل ذکر است که انتخب فیلتر تا اندازه زیادی به نوع خشککن مورد استفاده در مرحله بعدی بستگی دارد. فیلترهای خلاء گردان میتوانند ظرفیتهای تولید بالایی داشته باشند (و کاهش درهزینه کارگر)، اما کیکی را شامل ۳۵% رطوبت تولید میکنند. انواع جدید فیلتر پرس های با فشار زیاد میتوانند محصولی شامل ۲۴% رطوبت و فیلترهای لولهای نیز محصولی با ۱۸-۱۶% رطوبت میدهند. در مورد فیلترهای لولهای،کیکی حاصل میشود که برای بیشتر مشتریان قابل قبول است (بخصوص برای پر کردن کاغذ) و بنابراین مرحله خشک کن حذف میگردد.
۳- عملیات خشک کردن و خشک کنها
انواع تجهیزات متداول جهت خشک کردن کائولن عبارتند از : خشک کنهای نواری (Converyer Dryers)، خشک کنهای آپرون (Apron Dryers)،خشک کنهای گردان،خشک کنهای استوانهای و خشک کنهای با بستر معلق، در سالهای ایر دو نوع جدید خشک کنهای افشانگی و خشک کنهای سریع بوئل محبوبیت فراوانی کسب کردهاند. خشک کنهای گردان با حرارت غیر مستقیم بطور تیپیک ۲۳ متر طول و ۳ متر قطر دارد و، ظرفیت تبخیری آنها در حدود ۲ تن بر ساعت و ظرفیت تولیدی آن ها ۱۰ تن بر ساعت میباشد. مراحل اساسی کار عبارتند از : پخش کردن پالپ بصورت قطرات کوچک، اختلاط قطرات با گازهای گرم، خشک کردن قطرات و بازیابی مواد جامد. پخش مواد جامد. برای پخش کردن پالپ میتوان با هر یک از انواع این خشک کن، از افشانک دیسکی یا انژکتوری استفاده کرد. گفته میشود که خشک کردن بصورت افشانگی احتمال بوجود آمدن ذرات سختی که ضمن فرآیند خشک کردن شکل میگیرد را کاهش میدهد
در صنایع معدنی، عمدهترین کاربرد خشککنهای افشانکی در مورد کائولن است که معمولاًمتشکل از ذراتی عمدتاًکوچکتر از ۲ میکرون است. کیک فیلتر با افزایش مقدار کمی پلی فسفات سدیم (بعنوان عامل متفرق کننده) بصورت پالپ درمیآید و توسط پمپ به خشککن منتقل میشود خشک کنهای افشانگی انعطاف پذیری سایر خشککنها را ندارند و برای خشک کردن مواد بصورت کیک فیلتر مناسب نیستند، بلکه باید مواد را به حالت پالپ به آنها منتقل کرد.
نوع دیگر تجهیزات خشک کردن که در صنعت استفاده میشود، خشک کنهای «بابستر سیال» هستند که مخصوصاً برای خشک کردن محصول بصورت پلت مناسبند و نیز آسیای ساینده هربرتؤ که در آن ذرات رس بوسیله تیغههای گردان درون اتاقکی که چرخه هوای گرم در آن وجود دارد به پودر دانهریزی تبدیل میشود.
اگر یک مشتری رس پودر شده لازم داشته باشد، محصول خشک کن میتواند به داخل آسیا که با هوای گرم جاروب میشود وارد گشته که در آنجا هم آسیا شده و هم رطوبت آن به ۱% تقلیل مییابد. محصولی با ۱% رطوبت کاملاًبصورت گرد و غبار قابل پراکنده شدن است و لذا باید بستهبندی شود. در مورد خشک کردن نکات زیر قابل اشاره است:
٭ رس خشک با کیک فشرده شده،جهت دستیابی به محصولی با ۲۵% رطوبت و یا با پالپ برای افزایش غلظت آن از ۶۵-۵۵% به ۸۰-۷۰% جهت کاربرد در صنعت کاغذ مخلوط میگردد.
٭ کیک فیلتر همچنین میتواند به شکل نودول بیرون داده شود، سپس خشک شده آن آسیا میگردد تا محصولی که رس اسیدی نامیده میشود بدست آید.
٭ اکثر کاخانجات بزرگ، بیشتر از یک روش خشک کردن در اختیار دارند و میتوانند خط تولید را به تناسب نیاز مشتری به نوع خاصی از محصول تمام شده تنظیم کنند.
تجهیزات عمده مورد استفاده در فرآوری کائولن به روش تر
۱) کالاسیفایرهای جامی
۲) روشی که برای آرایش کائولن در غرب کارولینای شمالی، جورجیا و فلوریدا بیشتر بکار رفته است استفاده از کلاسیفایر جامی است. این کلاسیفایر از طرفی به شکل جام تشکیل شده است. کائولن به حالت پالپ از قسمت مرکزی جام وارد میشود و در این قسمت ذرات درشت تهنشین میشوند و کائولن آرایش یافته به آرامی از پیرامون جام سرازی میشود.
ابعاد جام بستگی به حجم پالپ اولیه و ابعاد کوچکترین ذراتی که باید تهنشین شوند دارد. ذرات تهنشین شده توسط تیغههایی که به کمک تعدادی بازو به آرامی دوران میکنند. به طرف مرکز جام هدایت شده و از دریچه ته ریز خارج میشوند. سپس برای بازیابی کائولن باقیمانده در بین این ذرات،آن ها را با آب صافی شستشو میدهند و با عبور مواد از زیر تعدادی دوش آب عملیات شستشو را کامل میکنند، بدین ترتیب میتوان به دو محصول قابل استفاده،یکی کائولن عاری از ماسه و دیگری ماسه عاری از کائولن دست یافت.
۲)هیدروسیکلون ها
چنانچه آزاد کردن کائولن از ناخالصی های همراه، مستلزم خرد کردن ماده اولیه تا ابعاد کوچکتر باشد، به منظور تسریع در جدا شدن ابعادی ذرات، از وسایلی استفاده میشود که براساس نیروی گریز از مرکز کار میکنند. رایجترین وسیله از این نوع هیدروسیکلون است. این وسیله از ظرفی استوانهای – مخروطی تشکیل شده است که مواد به حالت پالپ به طور مماسی از قسمت استوانه وارد آن میشوند و در نتیجه حرکت استوانهای درشتترین ذرات که معمولاً ناخالصی های همراه کائولن هستند، به جداره مخروطی شکل ظرف چسبیده و خروج آنها از دهانه زیرین ظرف که در رأس مخروط قرار گرفته است (ته ریز هیدروسیکلون) خارج میشوند. بسته به نوع ماده اولیه و مشخصات مورد نظر در محلول آراسته نهائی میتوان سرریز هیدروسیکلون را برای بهتر کردن کیفیت آن طی یک یا چند مرحله دیگر توسط هیدروسیکلون آرایش داد و یا برای بازیابی کائولن باقیمانده در ته ریز هیدروسیکلون، این بخش را در هیدروسیکلون دیگر آرایش داد. کوچکترین حد جدایش قابل دستیابی در هیدروسیکلونها در حدود ۵ میکرون است.
۳) دستگاه گریز از مرکز (سانتریفوژ)
دستگاههای گریز از مرکز به عکس هیدروسیکلون ها که دستگاه هایی ساکن هستند، از ظرفی به شکل جام، استوانه و یا مخلوط که با سرعتی زیاد (در حدود rpm 3500) حول محور خود گردش میکند. تشکیل شدهاند. در دستگاه گریز از مرکز، به علت نیروی گریز از مرکز شدیدی که بر ذرات وارد میشود، سرعت تهنشین شدن ذرات افزایش پیدا میکند و میتوان ضمن صرفهجویی قابل توجه در فضا و دستمزد، کائولن را در ابعاد خیلی کوچک طبقهبندی کرد. رایجترین نوع این وسیله از ظرفی لولهای شکل تشکیل شده است که در داخل آن مارپیچی با سرعت کمی متفاوت با مخروط دوران میکند.
ماده اولیه به حالت پالپ از قسمت مرکزی وارد میشود. ذرات دانه درشت تحت نیروی گریز از مرکز به طرف جدار داخلی ظرف هدایت و توسط مارپیچ از قسمت رأس مخروط خارج میشوند ذرات دانه ریز هم که عمدتاًمتشکل از کائولن هستند از قسمت قاعده مخروط بیرون میآیند. کوچکترین حد جدایش قابل دستیابی در دستگاه های گریز از مرکز در حدود چند میکرون است. این وسیله کم حجم و با ظرفیت زیاد است. انواع بزرگ آن که تنها سطحی معادل ۱۴ متر مربع را اشغال میکنند، میتوانند ۱۰۰ تن ماده اولیه در ساعت آرایش دهند.
هدف از روش های فوقالذکر در حقیقت طبقه بندی مواد خصوصاً در دانهبندی خیلی کوچک است. با توجه به طبیعت کائولن و خاک های رسی که بسیار ریزدانهاند، میتوان با جدا کردن ذرات درشت کیفیت کائولن را افزایش داد.
۴) جدا کننده مغناطیسی با شدت زیاد
ناخالصیهای رنگی در کائولن نظیر آناتاز، روتیل، گوتیت،هماتیت، میکا و پیریت خاصیت مغناطیسی ضعیفی دارند، لذا این ناخالصی ها را باید توسط جدا کنندههای مغناطیسی با شدت زیاد حذف کرد. جدا کنندهای که برای آرایش مواردی با ابعاد در حد میکرون (مشابه کائولن) قابل استفاده است،جدا کننده مغناطیسی با گرادیان زیاد است که فیلتر مغناطیسی نام گرفته است. در این جدا کننده در یک میدان مغناطیسی یکنواخت مقداری رشتههای باریک فرو مغناطیسی که حدود ۵ تا ۱۰ درصد فضا را اشغال میکنند، قرار داده شده است.
رشتههای مورد نظر در محفظهای که بطور تیپیک ۲۱۱ سانتیمتر قطر و ۵۰ سانتیمتر عمق دارند تعبیه شدهاند. در اطراف لبههای تیز این رشتههای بسیار ظریف میدان مغناطیسی شدیدی در حدود یک کیلو گوس را میتوان بدست آورد، محفظه مذکور توسط ۱۶ سیم پیچهای توخالی که هر یک شامل یک تن مس میباشند، احاطه شده است. و میدانی مغناطیسی باشدت ۱۵ تا ۲۰ کیلو گوس را ایجاد مینماید. توان الکتریکی مصرفی ۲۷۰ تا ۵۰۰ کیلو وات میباشد. واحدبزرگتر آن با قطر ۳۰۱ سانتیمتر قابلیت فرآوری ۱۳۰ تن بر ساعت کائولن را با ۳۰ ثانیه زمان توقف دارد و ۴۰۰ کیلو وات توان مصرفی آن است.
هنگام عبور ماده اولیه کائولن به حالت پالپ از فضای موجود در بین این رشتهها ذرات پارامغناطیسی فوقالذکر جذب آنها میشوند و محصول خارج شده عاری از آهن خواهد بود،کار این وسیله متناوب است،زیرا به تدریج سطح رشتهها از ذرات جذب شده پوشیده میشود، لذا بایستی پالپ ورودی و همچنین میدان مغناطیسی را قطع و با عبور آب صاف از داخل دستگاه، ذرات پارامغناطیسی را خارج کرد. این عملیات طی یک سیکل تقریباً۲۰ دقیقهای انجام میشود. تکنیک جدایش مغناطیسی پیشرفت قابل ملاحظهای در صنعت کائولن بوجود آورده و فرآوری کائولن هایی با عیارهای پایینتر را ممکن ساخته است. در نتیجه این عملیات ذخایر اقتصادی کائولن در جنوب شرقی ایالات متحده به بیش از دو برابر افزایش یافته است.
۵) فلوتاسیون
حذف ناخالصی های تیتانیم- آهن از رس بوسیله فرآیند فلوتاسیون معمولی کاری مشکل است. قطر این ناخالصی ها معمولاً کوچکتر از ۲ میکرون بوده و مقادیر کمی از آن ها در رس وجود دارند. در صنعت مدت زیادی است که دشوار فلوتاسیون ذرات کمتر از ۱۰-۵ میکرون توسط سلولهای فلوتاسیون مشخص شده است و یک دلیل ارائه شده برای این امر است که حباب های تولید شده در سلولهای فلوتاسیون معمولی برای جذب ذرات ریز، بسیار بزرگ هستند و بنابراین سرعت فلوتاسیون پایین است. غیرعادی نیست. هر آزمایش کامل فلوتاسیون در آزمایشگاه ۴۵ تا ۲۰۰ دقیقه جهت حذف ناخالصی های تیتانیم – آهن از رس طول طول بکشد، فرآیند فلوتاسیون حامل تکنیکی است که برای شناور کردن ذرات ریز آناتاز از رس با استفاده از یک سلول فلوتاسیون معمولی طراحی شده است، در این تکنیک ذرات حامل که قبلاً آماده شدهاند، در اندازههای بهینه (نظیر کلسیت زیر ۳۲۵ مش) به خط فلوتاسیون اضافه میشوند و بدین ترتیب آنها میتوانند ذرات آناتاز حامل بوسیله یک کلکتور مناسب نظیر اسیدهای چرب، روغن تال (Tail oil )آماده شده و در یک مخرن جداگانه با گل آب رس مخلوط میگردند. بدین ترتیب ذرات آناتاز آبران (هیدورفوب) طی یک مکانیزم جذب هیدروفوبیکی به ذرات کلسیت میچسبند و مزیت دیگر این فرآیند (بهبود سینیتیک فلوتاسیون) را نشان میدهد. به این دلیل است که درخشندگی کائولن مورد عمل را در بازیابی بالاتر بهبود میبخشد.
پترونات کلسیم نیز در این فرآیند استفاده میشود که نقش اول آن ممکن است فعال کردن آناتاز باشد این ماده شامل ۴۱% کمپلکس سولفونات کلسیم و ۵۹% نفت است و همچنین بعنوان یک امولسیون ساز برای کلکتور نفتی انجام وظیفه میکند. مقدار زیادی نیز سولفات آمونیوم (Kg/ton 27/2) بکار میرود اما نقش آن در این فرآیند مشخص نیست. اضافه کردن کفساز نیز لازم نیست زیرا هم اسید چرب و هم سولفونات نفت کف کافی را تولید میکنند.
آمادهسازی حامل کلسیتی کلکتور بسیار سادهتر است. کانی کلسیت (۳۲۵ مش) با روغن تال (Kg/ton 8/1) در حضور سرد سوز آور (Kg/ton 113/0) آماده میشود. مقدار کانی حاصل مورد استفاده از۳۰ تا ۲۰۰ درصد وزنی رس متغیر است. قسمتی از این کانی حامل بازیابی شده دوباره وارد خط میشود. کانیهای دیگری مثل کوارتز. باریت، سیلیس، گوگرد، فلوریت و… نیز ممکن است بعنوان کانی حامل مورد استفاده قرار گیرند، اما کلسیت به علت ارزانتر بودن و وفور بیشتر مورد استفاده قرار میگیرد.
پالپ آماده شده وارد سلولهای فلوتاسیون اولیه میشود و بخش شناور شده طی سه مرحله دیگر شسته میشود که محصول شناور شده نهایی عمدتاً آناتاز است. نمودار ساده نشدهای از فرایند فلوتاسیون کائولن با استفاده ازکلکتور کلسیتی در شکل آورده شده است.
فلوتاسیون حامل بطور موفقیت آمیزی بوسیله شرکت معدنی و شیمیایی « انگلهارد» از سال ۱۹۶۱ جهت تولید کائولن مورد استفاده در پوشش کاغذ با درخشندگی ۹۰ + بکار گرفته شده است. لیکن این فرآیند معایب زیر را نیز دارد:
۱- مصرف مواد زیادی برای آماده سازی کانی حامل مورد نیاز است.
۲-فرآیند فلوتاسیون در غلظت های پائینی از پالپ (کمتر از ۲۰% جامد) موثر است که طبعاً هزینه آبکشی را افزایش میدهد.
۳- کانی حامل اضافه شده باید اساساً از محصول رس حذف شده و جهت برگشتن به خط بازیابی گردد.
۴- حضور کانی حامل و مواد شیمیایی باقیمانده در رس اثرات زیان آوری روی محصول نهائی دارد.
جهت مطالعه مکانیزم فلوتاسیون حامل،پتانسیل های سطحی آناتاز، کائولینیت کلسیت در ۱/۱۰ = PH اندازهگیری شد. محققین دریافتند که آنها همه منفی و دارای مقادیر تقریباً مشابه هستند به همین دلیل امکان جاذبه الکتروستاتیکی بین آناتاز و کلسیت رد شد. نتیجه اینکه چسبندگی مزبور بوسیله واکنش هیدروفوبیک بین کانیهای موجود در کلکتور فراهم میشود. از آنجایی که کلکتور روی هر سه کانی جذب سطحی دارد، هیچ دلیل مشخصی برای فرآیند چسبندگی انتخابی بین آناتاز و کلسیت وجود ندارد. ولی محققین نشان دادهاند که پتانسیلهای سطحی کائولینیت پس از یک همزدن شدید کاهش می یابند. در حالیکه در مورد آناتاز تغییری در پتانسیلهای سطحی صورت نمیگیرد. لذا پژوهشگران حدس زدند که جذب کلکتور بر روی کائولینیت در مقایسه با آناتاز ضعیف میباشد. همان گونه که عنوان شده است،همزدن شدید ممکن است نقش مهم دیگری در فلوتاسیون حامل داشته باشد. ممکن است که همزدن شدید توسط فلوکولاسیون برشی را برای ذراتی که توسط کلکتور پوشانده شدهاند فراهم کند. این اثر اولین بار در سال ۱۹۷۵ توسط «وارن» مشاهده شد. بطور ساده فلوکولاسین مزبور موقعی رخ میدهد که انرژی همزدن شدید بر انرژی مانع چسبندگی غلبه کند.
«کاندی» (۱۹۶۹) فرآیندهای فلوتاسیونی را که گسترش داد که نیاز به کانی حامل ندارند. روال ساده این فرآیند دو قسمتی است، ابتدا گل آب کائولن توسط همزدنشدید با حداقل HP/ton 25 انرژی لازم آماده میشود، «کاندی» فهمید که این بهم ردنباعث از بین رفتن آلودگی سطحی که اختلاف اثر کلکتور بر روی ذرات متفاوت دو کانی را کاهش میدهد، موثر است. در بخش دوم خمیر رس درحضور فعال کنندهای که محلول در آب یک فلز قلیایی خاکی یا یک فلز سنگین است، آماده میشود.
«یانگ و دیگران» (۱۹۸۵)، فرآیند فلوتاسیونی را توسعه دادهاند که برای پرعیار سازی رس در غلظت های بالا طراحی شده است. مزیت های این فرآیند عبارتند از: هزینه آبکشی کمتر و بازدهی بیشتر. اصول اصلی این فرآیند شبیه به فرآیند فعالسازی «کاندی» است،جز آنکه گل آب رسی قبل از آمادهسازی در معرض یک رنگزدائی اکسیداسیون قرار میگیرند و یک پلی اکریلات محلول در آب قبل از فلوتاسیون بعنوان متفرق ساز به رس اضافه میشود.
فرآیند فلوتاسیون دیگری که باید در اینجا به آن اشاره شود فلوتاسیون روغنی است این فرآیند شبیه فلوتاسیون معمولی است فقط در یک موردتفاوت دارند و آن این است که در فلوتاسیون معمولی، بجای جمعآوری ناخالصیهای رنگی (آناتاژ) با استفاده از حباب هوا، از مایعات غیر محلول در آب استفاده میشود،بعد از آماده سازی و افزودن شیمیایی به رس مقداری نفتا یا مایعات غیرقابل حل در آب به پالپ افزوده میشود و با همزدن زیاد آن یک امولسیونی روغنی در آب بوجود میآید. وقتی همزدن متوقف میشود قطرات روغنهای آناتاز بر روی سطح میآیند که میتوان آنها را جمعاوری نمود. در مرحله بعد مایع روغنی یا میع نامحلول در آب برای استفاده مجدد بازیابی میشود. نمودار ساده شده این فرآیند در شکل نمایش داده شده است. از فرآیند فلوتاسیون روغنی برای ذرات خیلی ریز رس که فلوتاسیون معمولی عملکرد خوبی روی آنها ندارند، استفاده میشود میزان درخشندگی ۹۲ تا ۹۳ شامل رسهایی است که ۹۵% آنها کمتر از ۲ میکرون هستند. مهمترین عیب فلوتاسیون روغنی کنترل دقیقی است که باید روی آن انجام شود تا بازیابی خوب محلول حفظ شود، در ضمن بایستی مایع غیر محلول بخوبی بازیابی شده بطور که به اقتصادی بودن پروژه لطمه نزند.
۷)کواگولاسیون ـ فلوکولاسیون انتخابی
اگر چه فرآیندهای فلوتاسیون مختلف در حذف ناخالصی تیتانیم- آهن از رس های نسبتاً درشت دانه موفق بودهاند،لیکن توفیق کمی در مورد رسهای دانه ریز داشتهاند. بعنوان مثال فرآیندهای مختلف فلوتاسیون در مورد رس های نسبتاً درشت دانه جورجیا مرکزی موفق و در مورد رس های بسیار دانه ریز جورجیای شرقی تقریباً ناموفق بودهاند. کائولن جورجیای شرقی معمولاً بطور تقریبی به میزان ۹۰% ازذرات کمتر از ۲ میکرون و در حدود ۵۰% کمتر از ۲۵/۰ میکرون در حالت خام تشکیل یافته است. فرآیندهایی از کواگولاسیون و فلوکولاسیون انتخابی وجود دارند، که از اواخر دهه ۶۰ گسترش یافتهاند. شکرت «جی. ام. ام هابر» با استفاده از این روشها، رسی با درخشندگی ۹۰ + از ماده خام جورجیای شرقی از اوایل دهه ۷۰ تولید میکرده است.
با کنترل دقیقی محیط یونی در یک سوسپانسیون کائولن این مکان وجود دارد که کائولن را در حالت پراکنده نگهداشته و اجازه دهیم که ناخالصی های رنگی لخته شوند (فلوکولاسیون).
محیط مناسب یونی برای فلوکولاسیون آناتاز ممکن است از راههای مختلف مهیا شده باشد. شاید سادهترین حالت، ایجاد تفرق بیش از حد ذرات کائولن باشد که این عمل توسط متفلق سازهای شیمیایی میتواند انجام شود از جمله این متفرق سازها میتوان به پلی فسفات تتراسدیم و هگزامتافسفات سدیم اشاره کرد. وقتی مقدار مناسبی مواد شیمیایی وارد محلول شوند. ذرات ریز کائولن کاملاً متفرق شده و در این حالت ذرات آناتاز بهم چسبیده و لخته میشوند، ذرات لخته شده رش میکنند تا جائی که اندازه آن ها نسبت به ذرات کائولن قابل توجه میشود. در این حالت لختههای آناتاز در میان سوسپانسیون قابل تمیز است. لایه بالایی که کائولن خالص شده را در بر میگیرد و لایه پائینی که شامل آناتاز لخته شده است.
در فرآیندهای مختلفی که در بالا شرح داده شده، مقدار کمی از ناخالصیهای موجود در رس بطور انتخابی بهم چسبیده و لخته میشوند.
«مینارد» (۱۹۷۹) فرآیندی را گزارش کرد که در آن کائولینیت توسط یک پلیمر آنیونی با مولکول سنگین و پایدار، لخته میشود و ناخالصی های آهن و تیتانیم در سوسپانسیون باقی میمانند. لیکن مقادیری از ناخالصی های در رس گیر کرده، به همراه آن تهنشین میشوند. لذا باید این لختهها را با مخلوطکن قوی دوباره متفرق کرده، چند بار شست.
اگر چه فرآیندهای کواگولاسیون- فلوکولاسیون موفقیت خود را در حذف ناخالصی ها از رس های جورجیای شرقی که شامل ذرات بسیار ریز هستند ثابت کردهاند، ولی معایبی بشرح زیر از این روش گزارش شده است:
۱- عموماًبرای این فرآیند نیاز است که غلظت پالپ کمتر از ۲۰% باشد، لذا مقادیر قابل ملاحظهای آب باید جدا گردد.
۲- بازیابی محصول معمولاً بخاطر درگیر شدن رس در لختههای تهنشین شده، پایین است.
۳- پلیمر لخته ساز باقیمانده در محصول نهائی تاثیرات زیان آوری دارد.
۴- از آنجایی که رسها دارای منشاءهای گوناگونی هستند، لذا باید آزمایشات زیادی برای ایجاد محیط یونی مناسب جهت فلوکولاسیون انتخابی انجام داد.
۷) روش های بیولوژیکی
میکرو ارگانیسمها میتوانند با تاثیر بیولوژیکی که منجر به ایجاد محیطی اکسید کننده یا احیا کننده میشود، مواد خالصی را به حالت محلول در آورند. لازم به تذکر است که در نتیجه عوامل بیولوژیکی، عملی عکس نیز ممکن است انجام شود، یعنی ممکن است عناصر محلول تبدیل به ترکیبات غیر محلول شده تهنشین شوند. کمتر مادهای میتواند تحت تاثیر عوامل بیولوژیکی قرار نگیرد. تاثیر این عوامل بر روی ذخایر ذغالسنگ، گوگرد و فسفات از دیر زمان شناخته شده است، در سالهای اخیر نیز بررسی های انجام شده نشان داده است که سیلیکات ها نیز تحت تاثیر عوامل بیولوژیکی به حالت محلول در میآیند حتی کانیهایی که به عنوان غیر محلول شناخته شده بودند نمیتوانند در مقابل این عوامل مقاومت کنند.
میکروارگانیسمهای هتروتروپیک مختلفی قادر به انحلال آهن از کانیهای اکسیده آهن (لیمونیت،گوتیت و هماتیت) هستند. انحلال با تشکیل اسیدهای آلی و سایر متابولیتها به صورت عوامل کمپلکس و همچنین احیای آهن به طریقه آنزیمی و غیر آنزیمی است.با پرورش نوعی قارچ در ۳۰ درجه سانتیگراد در محیطی مغذی حاوی ملاس چغندر به عنوان منبع کربن و انرژی و استفاده از آن میتوان آهن موجود در کائولن را کاهش داد.
۸) الکترواسمز
یکی از روشهایی که در دهه دوم و سوم قرن حاضر در اروپای غربی بکار میرفت، روش الکترواسمز است. این روش با توجه به هزینههای زیادی که دارد (معادل Kwh 88 به ازای هر تن ماده اولیه)، تنها در صورت در اختیار داشتن انرژی ارزان قابل استفاده است.
در این روش از باردار شدن مواد جامد در آب و جذب آنها روی الکترودهایی با بار مخالف استفاده میشود. نخست تصور میشد که در شرایطی از محیط که ذرات کائولن با منفی دارند، ناخالصی های همراه آن مثل کوارتز، میکا و کانیهای آهن بار مثبت دارند، بنابراین ذرات کائولن روی کاتد جمع میشوند. حال آنکه چنین نیست بنابراین این روش میتواند برای فیلتراسیون الکتریکی ذرات خیلی دانه ریز بکار رود.
بر مبنای این روش، واحدهایی هنوز در انگلستان در حال کار هستند در این واحدها ماده اولیه کائولن، پس از به تعلیق در آمدن در آب، ابتدا از حوضچههایی عبور داده میشود و بدین ترتیب ذرات دانه درشت آن جدا میشودن و بدین ترتیب ذرات دانه درشت آن جدا می شوند سپس به داخل کانالهای طویلی بطور ۱۶۰ متر، عرض ۳/۱ متر و عمق ۵/۰ متر هدایت میشود. در این کانال ها که مدت توقف مواد در آنها ۷۰ دقیقه است، بخشی از کائولن با غلظت وزنی ۳۱% تهنشین میشود که پس از خشک شدن به عنوان محصول درجه ۲ در صنایع کاغذسازی مصرف میشود. سرریز کانال ها که دارای محصول دانه ریز و با عیار بسیار زیاد است، به دستگاه الکترواسمز هدایت میشود. این وسیله تشکیل شده است از بدنهای از جنس شبکهای فلزی به شکل نیم استوانه در نقش کاتد و محوری گردان در داخل آن بطول ۵/۱ متر و قطر ۶/۰ متر در نقش آند.
این وسیله با جریانی یک سو بشدت ۷۰ آمپر و ولتاژ ۱۰ ولت تغذیه میشود. ذرات کائولن روی آند میچسبند و لایهای به ضخامت ۳ میلیمتر تشکیل میدهند که از روی آند تراشیده میشود. در این روش تنها ۹% کائولن در آب خروجی باقی میماند.
روش های افزایش درخشندگی کائولن
روش هایی جهت کمبود کیفیت نوری کائولن خصوصاً در دو دهه گذشته برای افزایش درخشندگی کائولن گسترش یافتهاند. نظر به این که روش های فوق (روش های افزایش درخشندگی خود نیز نوعی از متدهای فرآوری کائولن میباشد لذا میتوان روش های افزایش درخشندگی را در زمره روش های فرآوری آورد). بطور طبیعی و بدون فرآوری،رسی با کیفیت خوب میتواند درخشندگی در دود ۷۵ تا ۸۵ ISO داشته باشد. مقادیر درخشندگی ۹۰ و بالاتر از آن با استفاده از چند تکنیک پر عیار سازی ویژه قابل دسترسی است. این تکنیک ها بقرار زیرند:
۱- آسانترین این روش ها رنگ زدایی است. فرایند شستشویی که در آن کانیهای آهندار بوسیله افزودن یک ماده احیا کننده (معمولاًهیدروسولفیت سدیم) در PH پایین (که میتوان با افزودن اسید سولفوریک و یا سولفات آمونیوم به آن رسید) حذف میشوند.
۲- از طریق توسعه اولترا فلوتاسیون، جداسازی کانی های فوقالعاده ریز امکان پذیر شده است. در این روش، یک کانی حامل را برای حمل ذرات بسیار دانه ریز کانههای آهن و تیتانیم بکار میبرند که با فلوته شدن آنها درخشندگی محصول به حدود ۹۰ میرسد.
۳- متورق سازی فرآیند دیگری است که طی آن ذرات بزرگ کائولن (که شامل تودههایی انباشته از صفحات شش گوش هستند) به ذرات نازک اما با صفحات مجزای عریض میشکنند. این ذرات با ایجاد صفحات جدید تمایل به سفیدی بیشتری نسبت به یک رس طبیعی پیدا میکنند. صفحات نازک بدست آمده از متورق سازی، یک پوشش عالی را برای کاغذ با وزن کمتر فراهم میکنند.
۴- تکلیس: اگر چه تکلیس کائولنهای درشت و رس های کائولینیتی عمل متداول برای تولید شاموتها و کلوخههای نسوز (برای مثال بعنوان فرایندی جهت افزایش خواص نسوزندگی) میباشد، ولی این فرایند میتواند همچنین بر روی ذرات ریز و سفیدتر کائولن جهت بهبود و افزایش درخشندگی و نیز بهبود سختی، ماتی و… اعمال گردد. این کائولن جهت بهبود و افزایش درخشندگی و نیز بهبود سختی، ماتی و… اعمال گردد. این کائولنه ا بطور فزایندهای در لاستیک، رنگ های کائوچویی و پلاستیک ها مورد استفاده قرار گرفتهاند.
دو نوع کائولن که اعمال حرارتی بر روی آنها انجام که است برای دستیابی به خواص پوشش ویژه گسترش یافتهاند. این دو نع کائولن ا عبارتند از :
۱- کائولن هایی که بطور ناقص تکلیس شدهاند.
۲- کائولن هایی که بطور کامل تکلیس شدهاند.
دسته اول تا جایی حرارت داده میشوند که گروههای هیدروکسیلی که در ساختمان بلور کائولینیت وجود دارند، بصورت بخار آب خارج شوند. درجه حرارت مزبور عموماً در حدود ۶۵۰ تا ۷۰۰ درجه سیلیس (بسته به میزان مادهای که مورد تکلیس قرار میگیرد) میباشد. این فرایند حرارتی رنگدانه را تولید میکند، که هنگام مخلوط شدن با پوشش دهندهها وزن مخصوص موثر کمتری دارد. بعلاوه، قدرت پراکندگی نور این محصول نسبت به رس های پوششی عادی بیشتر است. هنگامیکه این کائولن بعنوان مادهای افزودنی به پوشش دهنده، کاغذ بکار میروند تا کشسانی و ماتی را در برگههایی که وزن اولیه کمی دارند افزایش دهند،حجیم بودن آنها یک مزیت بشمار میرود. این محصول گرانروی بالائی داشته و لذا نمیتواند به تنهایی بعنوان پوشش دهنده در ماشینهای چاپ باعث سرعت بالا استفاده شود، ولی میتواند تا حد ۴۰% کل رنگدانه را در ترکیب با دیگر انواع کائولنها تشکیل دهد. افزودن این کائولن های ناقص تکلیس شده به ترکیب پوشش دهنده سبب افزایش ضخامت پوشش، افزایش ماتی، کاهش عمدهای درافت درخشندگی و ماتی هنگام نورد کردن، بهبود پذیرش جوهر و یکنواختتر شدن چاپ های چهار رنگ میشود. کائولن ها کاملاً تکلیس شده، تا دمایی بین ۱۰۰۰ تا ۱۰۵۰ درجه سانتیگراد حرارت دیدهاند. تلفیق دانهبندی ریز و فرآوری های خاص به کاهش سایندگی آنها تا حدی قابل قبول کمک میکنند. اگر چه خواص فیزیکی محصول تکلیس شده ظاهراًتغییر عمدهای نمیکنند، اما تکلیس و فرآوری، درخشندگی و مشخصات پراکندگی نور را افزایش میدهند.
۵. فیلتراسیون مغناطیسی با نوع جدید جدا کنندههای مغناطیسی، بحث های زیادی را در سالهای اخیر برانگیخته است و این فرآیند بخصوص در حذف ذرات ریز آهن، تیتانیم و میکا و… موثر است و میتواند هم برای تولید رس های فوقالعاده سفید از ماده خام معمولی و هم برای افزایش عیار رس های حاشیهای کم عیار معدنی استفاده شود. با این روش مقدار مواد شیمیایی بکار رفته جهت درخشان کردن محصور میتواند بطور عمدهای کاهش یابد.
- فرآیندهای آینده: پیشبینی در مورد فرآیندهایی که ممکن است امروز فقط در مرحله ترسیم بر روی کاغذ باشند، مشکل است. ولیکن جستجو و پژوهش برای یافتن فرآیندهای موثر جهت افزایش درخشندگی و دیگر مشخصات رس ادامه خواهد داشت. تکنیک های فعلی بهبودخواهند یافت (برای مثال فیلتراسیون مغناطیسی بعنوان یک فرآیند تجارتی هنوز در مرحله، رشد خود بسر میبرد و برای توسعه فلوتاسیون نیز جای بیشتری وجود دارد). فرآیند درو مایعی در حال توسعه بوسیله (شرکت اقتصادی Ecc )یکی از فرآیندهای بالقوه است که میتواند در آینده بکار گرفته شود.
روش های کاهش هزینه انرژی در فرآوری کائولن
در روش های آماده سازی رس انرژی زیادی مصرف میشود، لذا در سال های اخیر تحقیقات قابل ملاحظهای جهت یافتن روش هایی که هزینههای انرژی را کاهش دهد، انجام شده است. برخی از آنها به قرار زیرند:
- اولین و آسانترین روش، فروش رس بصورت پالپ میباشد که در نتیجه مرحله خشک کردن محصول ضروری نخواهد بود. این کار باید برای مشتریانی انجام گیرد که آمادگی پذیرش پالپ را دارند البته در این صورت اگر چه میزان هزینه به لحاظ عدم صرف انرژی جهت خشک کردن کاهش مییابد، ولیکن هزینه حمل آب اضافی را باید در قیمت تمام شده منظور کرد.
در اینجا مسیری که پالپ طی میکند شبیه مسیر خشک کردن است و شامل آسیا کردن نیز میباشد. مقدار کمی متفرق ساز به رس افزوده میشود که در ادامه کار در یک مخلوطکن با سرعت زیاد مخلوط میگردد. سپس کمی آب افزوده شده و نتیجتاً پالپی با ۷۰ – ۶۵% جامد ساخته میشود. پالپ حاصل به محل مورد نظر خریدار از طریق جاده یا راه آهن با توسط کشتی حمل میگردد.
- روش دوم کاهش هزینههای خشک کردن استفاده از تکنیک های فشرده کردن با فشار بالا میباشد که در نتیجه نیازی به خشک کردن متداول نخواهد بود.
اساس کار فشرده کردن با فشار بالا شبیه پرس معمولی است با این تفاوت که فشار در حدود۷۰ باز است و توسط پرس های پیستونی سریع به اجرا در میآید. کیک ها سخت بوده به سهولت تخلیه میشوند و لذا سیستم میتواند خود کار عمل کند. رطوبت کیک ۲۵% (قابل مقایسه با ۳۵ – ۳۰% برای پرس های با فشار معمولی) است و بنابراین میتوان بعنوان خوراک مستقیماً به خشک کن منتقل شود.
خط تولید بدون بار برگشتی سادهتر بوده و نیز گرد و غبار محصول داخل واحد خشک کننده را کاهش میدهند. یک مقایسه انرژی با مراحل فیلتراسیون، مخلوط کردن و خشک کردن معمولی نشان میدهد که سیستم فشار بالا در حدود ۵۳ درصد انرژی برای سیستم فشار پایین را بکار میبرد.
- سومین پیشرفت در شرکت اقتصادی Ecc کاربرد پرس لولهای است. همانطور که از نامش پیدا است این پرس شامل یک لوله بیرونی است که با یک لایه لاستیکی قابل انعطاف در سطح داخلی آن جفت شده است. لولهای با قطر کوچکتر بصورت هم محور با لوله بیرونی سوار شده است. بر روی لوله اخیر روزنههائی فیلتر دار تعبیه شده و توسط نگهدارندهها و پارچه، فیلتر روی سطح خارجی ثابت شده است. لوله داخلی یا شمع قادر است درون لوله بیرونی بطور قائم حرکت کند.پالپ رس با حدود ۲۵ درصدجامد بداخل فضای حلقوی بین پارچه، فیلتر و جدار لاستیکی هدایت میشود. وقی چرخه پرس کردن تمام میشود یک انفجار هوا در پشت پارچه فیلتر رخ میدهد. کیک فیلتر که در حدود ۱۸ درصد رطوبت دارد و متورم شده بطرف خارج حرکت میکند، رس در اینحالت سخت، قابل حمل و عاری از گرد و غبار است زمان پرس کردن بسته به دانهبندی رس متفاوت است اما اگر فرایندتمام اتوماتیک باشد تغییرات مناسب در زمان چرخه به راحتی میتواند اعمال گردد.
- فکری نو در مورد فیلتراسیون با استفاده ازاصل الکتروفورزی (مهاجرت بارهای الکتریکی) در یک محیط الکتریکی ارائه شده است (چاپک و دیگران ۱۹۷۴) ذرات کائولینیت که در PH بالاتر از ۳ دارای بار منفی هستند توسط فضای یونی بارهای مخالف احاطه شده یک دو لایهای اکتریکی تشکیل میشود. در یک محیط الکتریکی، ذرات رس بسمت آند حرکت میکنند در حالیکه یون های با بار مخالف در این فضای یونی بطرف کاتد میرود. وقتی ذرات به آند میرسند روی سطح جدار آند که برای محافظت از آند نصب شده یک کیک فیلتر شکل میگیرد. کیک آندی مزبور مجدداً بوسیله، فشار الکترواسمز آبکشی میشود این عمل طی مکانیزمی رخ میدهد که در آن آب اضافی از طریق لولههای موئین کیک با بار منفی به بیرون پمپاژ میشود. طبق نظر «بولینگر» فشار الکترواسمزی تولید شده در کیک فیلتر ممکن است بسیار بالا باشد، طوری که میتواند به فشار موثری در حدود ۷۰ بار برسد. اتاقک کاتد که با پارچه،فیلتر پوشیده شده جهت کمک به فیلتراسیون تحت خلاء قرار دارد.
ناخالصی های کائولن و ضرورت فرآوری آن
مرغوبترین کائولن، نوعی است که حداکثر دارای ۲۰ درصد ناخالصی باشد، به همین جهت باید به منظور استفاده در صنایع مصرف کننده، کائولن بطور معمول دارای ۴۸ درصد سیلیس و ۳۷ درصد آلومین و حدود ۴۶/۰ درصد اکسید آهن، ۰۶/۰ درصد اکسید کلسیم و ۵/۱ درصد اکسید سدیم و پتاسیم است. وجود لنزهای آهن دار و سنگ های ولکانیکی آندزیتی تا بازالتی فلدسپات تجزیه نشده سبب کاهش کیفیت کائولن میگردد.
از آنجایی که کائولن موارد مصرف متعددی دارد و صنایع مختلف برای تولید محصولات خود نیاز به کائولنهایی با مشخصات متفاوت دارند،لذا این کانه باید در طی مراحل مختلف و در جهت اهداف و تأمین خوراک مورد نیاز صنعت فرآوری گردد.
فرآوری یا کیفیت کائولن، بستگی مستقیم به میزان درصد آلومین دارد. یعنی هر چه آلومین آن بالاتر باشد. کائولین مرغوبتر و برعکس هر اندازه سیلیس آن بیشتر باشد، از اهمیت کمتری برخوردار است. بطور کلی در تغلیظ کائولن توجه به نکات زیر حائز اهمیت است.
٭ ناخالصیهایی که مقادیر آنها نباید از حد معینی کمتر یا بیشتر باشد. بطور مثال حد قلیایی کائولن در حالت عمومی نباید بیشتر از ۵/۱ درصد باشد.
٭ ناخالصی هایی که مصرف آنها در بعضی از صنایع مضر و در صنایع دیگر چندان اهمیتی ندارند نظیر ناخالصیهایی رنگ و میکا که در مصارف نسوز اهمیت ندارند.
٭ اندازه ذرات و دانهبندی آن ها، شفافیت،مقدار انقباض، میزان نسوزی و مقاومت گسیختگی ویسکوزیته، مقاومت الکتریکی، میزان شکلپذیری، مقدار آلومینیوم، کوارتز، اکسید آهن و تیتان از موارد قابل توجه در مصرف کائولن در صنایع مختلف هستند.
بدیهی است میزان ناخالصی در معادن مختلف متفاوت میباشند، لذا نحوه فرآوری و حذف این ناخالصیها نیز متفاوت خواهد بود.
تغلیظ کائولن عبارتست از جدا کردن ناخالصیها از قبیل زاج، گچ، پیریت و فلدسپات های تخریب نشده و… که این ناخالصی را اصولاًبه دو روش خشک و مرطوب میتوان خارج نمود.
بعضی از عناصر مزاحم بصورت ناخالصی همراه کائولن برای صنایع مختلف بشرح زیر هستند:
٭ صنعت لاستیکسازی: زاج، هوموس به عنوان ماده همراه
٭ صنعت کاغذسازی: هوموس و کوارتز، زاج به عنوان ماده همراه
٭ صنعت سرامیک و چینی سازی: زاج و اکسید آهن
٭ صنعت پلاستیک سازی: سایر اکسید آهن و دانههای کائولینی غیرفلسی
همچنین وجود پیریت اضافی در کائولن مضر بوده که از طریق اضافه کردن اسید سولفوریک PH محیط را به حدود ۳ رسانده و آن را جدا میکنند.
عمل جدا کردن مواد مزاحم (مثل سدیم، پتاسیم، آهک) را کائولنشوئی گویند. کائولنی که خوب شسته شده باشد تنها ۴۹/۰-۳۲/۰% = 3Fe۲O۳ و ۰۸/۰-۰۵/۰% = Ti۲O دارد.
تغلیظ کائولن در جدا کردن ناخالصی هایی مانند زاج، آلونیت،گچ، پیریت، فلدسپات های دگرسان نشده تجلی مییابد. کل ناخالصیها را میتوان به دو روش خشک و مرطوب از کائولن جدا کرد. در تصفیه کائولن همه ناخالصیها از جمله ریگ و میکا باید حذف شوند. مگر در مواردی که کائولن برای مواد نسوز بکار میرود.
کانی های کائولن
- کائولینیت Kaolinit :
کائولن با نام کانی شناسی کائولینیت با فرمول شیمیایی H۴Al۲Si۲O۹در سیستم تری کلینیک و سختی حدود ۵/۲-۱، دارای ۵/۳۹ درصد Al۲O۳ ،۵/۴۶ درصد Si۲O و ۱۴ درصد آب بوده و وزن مخصوص ۶/۲ – ۱/۲ گرم بر سانتی مترمکعب و نقطه ذوب آن ۱۷۸۵ °C است. رنگ آن سفید مایل به زرد و گاهی هم کمی سبز یا آبی رنگ بوده وطعم خاک دارد و به صورت مرطوب، بوی شدید خاک می دهد. این کانی اغلب دارای پلاستیسیته بوده و عملاً در آب، اسیدهای سرد و رقیق، اسید کلریدریک و اسید سولفوریک گرم و غلیظ و ئیدروکسیدهای قلیایی نامحلول حل می شود.
اغلب ذخایر کائولینی در اثر هوازدگی و تجزیه سنگ های ولکانیکی حاوی سیلکات آلومینیوم بوجود می آیند. سنگ های گرانیتی، گنایس ها، کوارتز، پورفیری ها و همچنین رسوبات حاوی فلدسپات ها، میکا و زئولیت جهت ایجاد کائولینیت مناسب می باشند که در اثر هوازدگی و تجزیه شیمیائی مواد قلیائی و مقداری از SO۲ خارج شده و کوارتز و سایر کانی های همراه بصورت ترکیب باقی می مانند.
کائولن ممکن است نتیجه آلتراسیون هیدروترمال باشد. در این صورت، محلول هیدروترمال سردتر از ۳۰۰ درجه سانتی گراد در داخل سنگ های با فلدسپات بالا، سبب شستن یون های Ca++,K+, Na+ و سایر کاتیون ها و رسوب آنها با H+ بیشتر می شود. اغلب این گونه ذخایر در ارتباط با سیستم متئوریک هیدروترمال، که حرارت از سنگ های ولکانیکی مشتق می شود، می باشند.
ذخایر بزرگی از کائولینیت در منطقه CORNWALL انگلستان در خارجی ترین قسمت های سیستم هیدروترمالی، مرتبط با باتولیت های گرانیتی وجود دارند که به عمق چندین کیلومتر تشکیل شده اند.کائولینیت در مقایسه با ناکریت- دیکیت از نظم کمتری برخوردار است و به همین دلیل اندازه بلور و ذرات اندازه بلور و ذرات هالوزیت در مقایسه با بقیه کوچکتر است. کائولینیت در زون های هوازده و آلتراسیون سنگ های آذرین و دگرگونی به ویژه فلدسپارها تشکیل می شود.
- رس توپی:
رس توپی یک نوع سنگ رسوبی است که حاوی کائولینیت و مقدار جزئی ایلیت، کلریت، کوارتز و مونتموریونیت است. ذرات کائولینیت در رس توپی در مقایسه با سایر منابع رس دار کوچکتر است. مقدار کائولینیت رس توپی ۲۰ تا ۹۵ درصد، کوارتز آن ۱۰ تا ۷۰ درصد و ایلیت و کلریت آن ۵ تا ۴۵ درصد است. مواد آلی، مونتموریونیت، ترکیبات اهن، اکسید تیتان و نمک های محلول از جمله ناخالصی های رس توپی هستند. رس توپی بیشتر همراه با لایه های زغال دار است و از آن جا که ذرات ریز کانی های رسی را به همراه دارد، خاصیت شکل پذیری آن بسیار خوب است. رنگ رس توپی قهوه ای مایل به سیاه است و مصارف آن عبارتند از : سرامیکهای بهداشتی، چینی های الکتریکی، انواع کاشی ها، ظروف غذاخوری، صنایع دستی و دیرگدازها.
•هالوزیت:
هالوزیت نوعی کائولین است که به دو حالت آب دار و بدون آب یافت می شود و ترکیب نوع آب دار آن مشابه بقیه است و تنها دو مولکول اضافی آب دارد. تشخیص هالوزیت به کمک پراش اشعه ایکس امکان پذیر است. هالوزیت بیشتر در زون های آلتراسیون و بندرت در زون های هوازده ساپرولیت یافت می گردد. عمده مصارف آن در تهیه سیمان پورتلند و تهیه نسوزها و سرامیک است.
- دیکیت:
دیکیت نوعی کائولین است که در سیستم مونوکلینیک متبلور می شود و عمدتاً در زون های آلتراسیون تشکیل می شود. - ناکریت :
ناکریت نوعی کائولین است که در سیستم مونوکلینیک متبلور می شود. نحوه قرار گیری ورقه های کائولینیت در ناکریت منظم است و بر همین اساس بلورهای آنها بزرگترند و به سمت هالوزیت کاملاً بی نظم است (ناکریت- دیکیت- کائولینیت- هالوزیت). ناکریت کمیاب بوده و در زون های آلتراسیون تشکیل می شود.
- خاک رس آتشخوار :
بیشتر خاک رس آتشخوار از کائولینیت تشکیل گردیده، کائولین در آن به خوبی متبلور می شد و نظم مطلوبی در شبکه آن وجود دارد. خاک رس آتشخوار، علاوه بر کائولین حاوی اکسید و هیدروکسیدهای آلومینیوم نیز هست. هر نوع خاکی که دمای بیش از ۱۵۰۰ درجه سانتی گراد را تحمل کند و میزان AL۲O۳ موجود در آن قابل توجه باشد، به خاک رس آتشخوار معروف است. خاک رس آتشخوار به انواع شکل پذیر، نیمه شکل پذیر و بی شکل تقسیم می گردد. خاک رس آتشخوار، بیشتر در افق های پایین لایه های زغال دار پیدا می شود. مصرف عمده این خاک در تهیه آجرهای آتشخوار است که به شاموت معروفند. دیگر مصارف آن در ساخت قطعات کوره ها، دیگهای گرمابی و کاشی های نسوز است
مصارف عمده کائولن ، کاربرد بالکلی، آنالیز بالکلی معدن کاوان
مشخصات کیفی کائولن مورد مصرف هر صنعت به تبعیت از صفات مورد نظر محصول نهایی متغیر است. این تفاوت حتی در صنایع مشابه بعلت تغیرات شدید کیفی کائولن استخراجی و یا فرآوری شده معادن کاملاًمشهود است، ویژگی صنعت، محدوده تغییرات مورد قبول را تعیین مینماید و فرمول سازی مواد مصرفی یکی از رایجترین راه حلها در اینگونه صنایع است.
مرغوبترین کائولنها تا حدود ۲۰ درصد ناخالصی را دارا میباشند که به منظور کاهش این ناخالصیها بطرق مختلف فرآوری میگردد و در هر روش نوعی خاص از این ماده حاصل میشود و هر کدام مصرف ویژه خود را دارد که علاوه بر صفات خاص ژنتیکی، نوع فرآوری نیز محصول را از یکدیگر متمایز مینماید. کائولن کلسینه شده، کائولن شیته شده توسط آب، حرارت نخورده،پودر شده، دانه بندی شده و کائولن پر کننده و طبقهبندیهای مختلف کائولن از نقطه نظر نوع فرآوری میباشند.
کائولن در صنایع مختلف به عنوان ماده اولیه اصلی و در برخی دیگر به عنوان ماده جنبی در کنار سایر مواد بکار میرود. قیمت مناسب و ویژگیهای این ماده معدنی در هر صنعت جلوههای خاص خود را دارد.
دلیل کاربرد فراوان کائولن در صنعت، دارا بودن ویژگی های زیر است:
- پرکننده و پوشش دهنده مناسب
- از نظر شیمیایی در گستره وسیعی از تغییرات pH بدون تغییر باقی می ماند.
- به عنوان جذب کننده مناسب مرکب و رنگ ها.
- به عنوان سخت کننده در صنایع پتروشیمی.
- داشتن رنگ سفید که آن را به صورت ماده رنگی قابل استفاده می سازد.
- جلای خاص و قابلیت سفیدکنندگی.
- خواص کاتالیزوری.
- دارا بودن خاصیت پرکنندگی و پوششی بسیار خوب.
- نرم کننده سطح و غیرسایشی بودن آن.
- قابلیت اندک هدایت جریان الکتریسیته و گرما.
- ارزانی قیمت آن.
بیشترین مصارف کائولن در پر کننده، پوشش دهنده با جلای خاص و سفید کننده، منبسط کننده، ایجاد کننده مقاومت در مقابل سایش، رقیق کننده، سخت کننده در صنایع پتروشیمی، نرم کننده سطح و به عنوان کاتالیزور در صنایع مختلف،کاغذسازی، سرامیک، مرکب و رنگ سازی، دیرگداز، پلاستیک، لاستیک، دارویی، فایبرگلاس، صنایع نسوز، مصالح ساختمانی، حشره کش، جذب کننده، مواد پاک کننده، مواد غذایی، تهیه داروها، صنایع کشاورزی و تهیه کودهای شیمیایی است.در ایران از این ماده معدنی در آجرهای شاموتی، پوشش داخلی کوره ها، دیگ های گرمایی و کاشی نیز استفاده می شود.حدود ۵۰ درصد از کائولن در کاغذسازی به عنوان پرکننده و روکش (پوشش دهنده سطح)،۲۰ درصد در صنایع سرامیک و دیرگداز، ۱۰ درصد در لاستیک سازی به عنوان پرکننده و ۲۰ درصد در رنگ سازی پلاستیک استفاده می شود.قدرت جذب مرکب و پوشش دهندگی خوب و پر کردن سطوح ناهموار کاغذ از خمیر سلولز و ایجاد شفافیت در کاغذاز مزایای استفاده از کائولن در صنعت کاغذسازی میباشد.
- سنگ کائولن برحسب نوع پیوندهایش به دو گروه پیوند نرم و سخت طبقه بندی می شود:
مصارف سنگ کائولن با پیوند نرم عمدتاً در صنایع کاشی، چینی و سرامیک سازی است.
مصارف سنگ کائولن با پیوند سخت در صنایع لاستیک سازی و کاغذ سازی می باشد.
- کائولن معدن کاوان در رنگدانه:
کائولن که به عنوان رنگدانه مورد استفاده قرار میگیرد به نوع پرکننده و پوشش کاغذ تقسیم میشود که این تقسیمبندی براساس درخشندگی، اندازه ذرات و ویسکوزیته آن است. کائولن کانی پرکننده ارزان، سفید یا نزدیک به سفید است که در یک دامنه وسیع از PH خنثی است. غیر ساینده و اندازه ذرات کوچک ولی قابل کنترل، هدایت گرمایی و الکتریکی کم و درخشندگی خوب است، در کاغذ، پلاستیک، رنگ، لاستیک، چسب، بتونه و… کاربرد دارد.
ترکیب شیمیایی آن بحرانی نیست به جز اینکه در رنگ تاثیر میگذارد، همچنین جذب روغن یا نفت آن بویژه برای رنگ یا لاستیک مهم است. خواص فوق به همراه شکل دانهها، ویسکوزیته و PH به آن اجازه میدهد تا بهعنوان رنگدانه پوششی کاغذ بکار رود. درخشندگی، صافی و پذیرش جوهر در کاغذهای چاپ و نوشتاری، هنری و… از خواص آن است.
در پلاستیک، کائولن برای ایجاد سطح صاف، پایداری در جهات مختلف و مقاوت در برابر مواد شیمیایی مصرف میشود (PVC)، پلیاستر ترموپلاستیک، نایلون و….
- کائولن معدن کاوان کاغذسازی:
استفاده از کائولن در کاغذسازی باعث نرمی کاغذ خواهد شد و جذب جوهر، درخشندگی، ارزانی و پوشش مناسب از دیگر مزیت های استفاده از کائولن در صنایع کاغذسازی است.کاغذ حتی اگر خلل وناهمواری های بین الیاف سلولزی آن بوسیله پر کننده معدنی پر شده باشد به منظور استفاده در فرآیندهای کارهای چاپی مدرن، تا زمانی که پوشش سطح را نداشته باشد مناسب نیست. استفاده از پر کننده در خمیر کاغذ بخشی از شکاف ها و درزهای بین الیاف سلولز را پر کرده، لذا بسیاری از نقاط ریز مرکب چاپ در این نقاط بدرستی قرار نگرفته و کیفیت کار چاپ کاهش مییابد. پوشش سطحی در روی کاغذ باعث نرمی، جلاء و قدرت جذب مرکب چاپ میشود. پوشش مناسب باعث افزایش کاربرد کاغذ میگردد.
کائولن به سرعت در آب (حتی در آب های سخت) پراکنده شده و به وسیله ماشینهای مدرن پوشش دهنده، پوشش نازک به کاغذ داده میشود. کائولن پوششی مناسب برای کاغذهای پرجلا، کاغذهای سبک با پوشش LWC و کاغذهای مناسب گراور به روش غلتگی (افست) میباشد. در صنعت تولید کاغذ،کائولن مورد استفاده باید به سرعت در آب معلق گردد. اندازه ذرات و دانهبندی از اهمیت ویژهای برخوردار است. درجه روانی (ویسکوزیته) و درصد ذرات با ابعاد کمتر از ۲ میکرون دارای اهمیت بیشتر هستند.
کائولن پوششی درجه یک ۹۲ درصد ذرات آن کمتر از ۲ میکرون و درخشندگی آن حداقل ۸۷ درصد است. کائولن پوششی درجه دو ۸۰ درصد ذرات آن کمتر از ۲ میکرون ودرخشندگی آن حداقل ۵/۸۵ درصد میباشد.
بطور خلاصه میتوان خواص زیر را برای کائولن جهت مصرف در صنایع کاغذسازی در نظر گرفت:
الف ـ شفافیت: حداقل شفافیت برای مصرف کائولن بعنوان پر کننده ۸۰ درصد و برای رس بعنوان پوشش ۸۵ درصداست که این عمل در مقایسه با استاندارد شفافیت مشخص میشود.
ب ـ اندازه ذرات: دقیقترین روش برای تعیین اندازه ذرات و پراکندگی آنها به اصل استوک استوار است بعبارت دیگر از روی سرعت تهنشین شدن در سیال قطر ذرات کنترل میشود. تعیین اندازه ذرات از روی زمان نشست آنها انجام میگردد.
ج ـ ویسکوزیته: درجه روانی کائولن در پوشش اکغذ بسیار مهم است. در صنایع کائولن دو آزمایش ویسکوزیته انجام میگردد که عبارتند از HSV و LSV،که برای تعیین این دو مورد به ترتیب از ویسکازیمترهای هرکولس و فیلد براک استفاده میشود.
د ـ باقیمانده سرند: ۳۲۵ مش بعنوان مواد ساینده یا باقیمانده سرند مصطلح میباشد. طریقه عملی بدین صورت است که ۱۰۰ گرم نمونه را کوبیده و خوب مخلوط نموده توسط مواد شیمیایی پراکنده می نمایند. سپس وزین درصد مواد جامد را در مخلوط اندازهگیری نموده، مجموع باقیمانده روی سرند را وزن کرده و درصد آن را محاسبه مینمایند.
۳.کائولن معدن کاوان در رنگ سازی :
استفاده از کائولن در رنگ سازی پلاستیک سبب کنترل ویسکوزیته می شود. ۱۰ % کائولن در رنگ سازی مورد مصرف دارد و باعث بالا رفتن قدرت پوششدهی، روان کنندگی و پخشکردن رنگ میشود. در رنگ سازی از کائولن مرغوب و خالص به صورت ماده رنگی و پرکننده بهره می گیرند. در رنگهایی که با آب شسته میشِوند نیز انواع کائولن درشتدانه نوع مات و انواع کائولن ریزدانه نوع شیشهای را ایجاد میکنند.
جایگاه صنعت رنگ سازی در مصرف کائولن، همچون صنعت لاستیک سازی در طی سالیان اخیر بوده است. افزایش رقابت بین کربنات کلسیم و کائولن، باعث کاهش سهم مصرف کائولن بعنوان پر کننده در صنعت رنگ سازی بوده است. بیشترین میزان رشد مصرف کائولن در صنعت رنگ سازی در کشورهای ایالات متحده امریکا و اروپا بوده که حدود دو درصد در سال برآورد گردیده است. پیش بینی میشود که بطور کلی و در آینده نزدیک میزان رشد مصرف کائولن در این صنعت، یک درصد باشد. البته در صورت وجود رشد اقتصادی در کشورهای آسیائی همچون گذشته، این رشد به ۵/۱ درصد خواهد رسید.
اصولاً کائولن بعنوان یک بسط دهنده و ماده اصلی رنگ سفید بصورت جایگزین اکسید تیتانیوم در تولید رنگ مورد استفاده قرار میگیرد. کائولن کلسینه شده اصلیترین کائولن بکار برده شده در صنایع رنگسازی است روشن بودن رنگ ضمن ناشفاف بودن، از خصوصیات کائولن مصرفی در صنایع رنگ سازی است و مشابهت خاصی با کائولن مصرفی در صنایع کاغذ دارد. سطوح صاف کائولینیت، بویژه در صنایع رنگ سازی با آرایشی خاص بر روی یکدیگر قرار گرفته که موجب استقامت ورقه رنگ شده و به آن عمر طولانی میدهد. بزرگترین تقاضا برای کائولن در صنعت رنگ، ساخت رنگ های مات داخلی ساختمان است.
معمولاً تا ۱۰ درصد وزنی رنگ های براق را میتوان کائولن اضافه نمود. کائولنی که در رنگ سازی مصرف میگردد باید از نظر رنگ روشن و از حداقل ناخالصی برخوردار باشد. ضریب تعلیق بالایی در آب داشته و نمک های محلول آن پایین باشد. از نظر درخشندگی بین ۹۰-۸۰ درصد و ذرات آن ۸۰-۷۰ درصد زیر ۲ میکرون باشد.
- کائولن معدن کاوان در لاستیک سازی :
در صنعت لاستیک سازی نیز کائولن را به عنوان ماده پرکننده به کار می برند. کائولن مقاومت در برابر سایش و صلبیت آن را افزایش میدهد.از کائولن خالص و نرم در لاستیک های نرم نظیر کاشی های لاستیکی و کائولن ناخالص در تهیه در لاستیک های سخت نظیر پاشنه و کف در کفش ها و لاستیک خودرو ها استفاده می شود.
مصرف کائولن در صنایع لاستیکسازی در سال ۱۹۹۸ معادل ۰۸/۱ میلیون تن بوده است. در طی سالهای ۱۹۹۰ الی ۱۹۹۸ مصرف جهانی لاستیک از ۰۲/۵ میلیون تن در سال ۱۹۹۱ به ۶۱/۶ میلیون تن در سال ۱۹۹۸ رسید و این نشاندهنده رشد متوسط سالیانه ۹/۳ درصد در طی دهه ۹۰ میلادی بوده است. بر اساس گزارش راسکیل رشد سالیانه ۱ درصد برای آیندهای نه چندان دور جهت مصرف کائولن در این صنعت پیشبینی میشود. مصرف کائولن در صنایع پلاستیکسازی موجب کاهش قیمت لاستیک میگردد. چون کائولن از لاستیک طبیعی و یا الاستومر بسیار ارزانتر است. کائولن مصرفی در صنایع لاستیک از نوع کائولن مرغوب نمیباشد. در ایالات متحده امریکا، کائولن مصرفی در این صنعت از نوع تغلیظ شده بوسیله هوا میباشد. در صنایعی که ذرات درشت مزاحم است مانند صنایع لاستیک که بوسیله اکستروژن شکل داده میشوند. از کائولن کلسینه شده هم در صنایع لاستیک سازی بعنوان پوشش استفاده میگردد. از خصوصیات عمده کائولن مصرف در صنعت لاستیک سازی این است که ۵/۹۹ درصدذرات باید زیر ۴۴ میکرون باشند.
- کائولن معدن کاوان در سرامیکسازی:
۲۰ % کائولن به عنوان یکی از مواد اولیه و اساسی در صنایع کاشی، چینی و سرامیکسازی است. کائولن از انواع نسوزهای آلومینیایی است که میزان آلومینا در آن ها بسته به نوع آن ها متغیر است. انواع کم آلومینا کائولن تکلیسشده، فلینت (۴۵-۳۵%) و انواع پرآلومینا مانند آندالوزیت، کیانیت و سیلیمانیت (۶۰-۴۰%). قدیمیترین وشاید متداول ترین روش کاربرد کائولن در صنعت، استفاده از این کانه در ساخت انواع محصولات سرامیکی میباشد. گل چینی بیش از چهار هزار سال است که در ساخت سرامیک مورد استفاده قرار میگیرد. درصنعت سرامیک سازی از مجموعه روشهای فرمول سازی مواد، شکل دادن و روشهای حرارت دادن و پخت استفاده میشود.بنابراین دامنه تغییرات نوع کائولن مصرفی وسیع میباشد بعبارت دیگر نوع محصول و روش تولید نوع کائولن را تعیین مینماید.
کائولن بدلیل ترکیب خاص شیمیایی در صنعت سرامیک مورد استفاده قرار میگیرد در مقابل حرارت حالت شیشهای آن تغییر نمیکند و درخشندگی و شفافیت خاصی در محصول ایجاد مینماید. در تهیه سرامیک مهمترین عامل نسبت اختلاط کائولن، سیلیس و کمک ذوب (Flux) در بدنه سرامیکها میباشد. ویژگی کائولن مصرفی در صنعت سرامیک عموماً مربوط به ناخالصیهای زیانآور موجود در آن است که باعث تغییر رنگ محصول بعد از پخت میگردد. مهمترین و مضرترین ناخالصیها اکسید آهن میباشد. از دیگر عناصر مضر میتوان از مس، کروم و منگنز نام برد. این مشکل زمانی نمود پیدا میشودکه این مواد بصورت ریزدانه در رس قرار گرفته باشند، در اینصورت بصورت بدنه محصول پس از پخت ظاهر گردیده و در پخت بیسکویت چنانچه مقدار اکسیژن کوره پایین بیاید. اطراف لکه حفرههایی بوجود میآید. مقدار اکسید آهن مجاز در سرامیک بین ۶/۰ تا ۷/۰ درصداست. اکسید آهن در کائولن جهت ساخت پرسلان باید کمتر از ۵/۰ درصد باشد زیرا تیتانیوم با آهن در بدنه سرامیک عکسالعمل نشان میدهد و موجب کاهش شفافیت میگردد.درجه آلکالی بودن اثر خاصی بر روی شیشهای بودن محصول دارد،زیرا بدنه سرامیک را متخلخل مینماید. کائولنی که در پرسلان بکار میرود پتاس آن باید کمتر از ۵/۱ درصد و مقدار تیتانیوم و سیلیس آن حداقل باشد.
وجود بعضی از کانیها در کائولن مضر است،رسهای طبیعی متورم کننده مانند مونت موریونیت که آب را در شبکه خود نگهداری مینمایند در روانی و شکلگیری قالب اثر میگذارد.در صنعت سرامیک کائولن ریز دانه ترجیح داده میشود. زیرا ریزدانه بودن موجب افزایش پلاستیسیته و افزایش مقاومت بدنه خام میگردد. انتخاب نوع دانه بندی بسیار مهم است، اگر چه ریز و نرمه بودن کائولن درجه ریختهگری را کاهش میدهد ولی در طول پخت موجب انقباض میگردد. به منظور استفاده کائولن در صنایع سرامیک سازی، آزمایشات مدول شکست، میزان شکل پذیری، رنگ پس از حرارت و انقباض در طول حرارت، میزان قالب پذیری و تعیین ویسکوزیته بر روی کائولن انجام میپذیرد.
۶.کائولن معدن کاوان در نسوز:
کائولن کانی است که مصرف گستردهای در صنایع نسوز دارد.این کانی حاوی ۲۰ تا ۹/۴۵ درصد آلومینا بوده و همین امر استفاده آن را در صنایع نسوز امکانپذیر میسازد. نسوزها موادی هستند که در مقابل حرارت مقاوم بوده و ترکیب شیمیایی، شکل ظاهری و خواص مکانیکی آنها تغییر نمیکند. کائولن و خاک های کائولن دار کاربردهای وسیعی بعنوان نسوز دارند و مهمترین بازار استفاده آن در صنایع آهن و فولاد است، لیکن مصرف رس صنعتی بعنوان نسوز بعلت دسترسی آسان و قیمت مناسب نیز بسیار گسترده میباشد. میزان مصرف کائولن در صنایع نسوز در سال ۱۹۹۹ حدود ۴ میلیون تن بوده است. صنایع شیشه سازی نیز از دیگر صنایع مهم مصرف کننده کائولن بعنوان نسوز میباشد.
۷.کائولن معدن کاوان در پلاستیک :
مصرف کائولن در صنایع پلاستیکساز ی کاملاً شبیه مصرف در صنایع لاستیک است و نقش کائولن بعنوان پرکننده و بسط دهنده میباشد. کائولن در این صنعت با دیگر مواد خام به رقابت پرداخته است. با افزایش قیمت نفت در دهه ۱۹۷۰، بازار مصرف کائولن و سایر پر کنندهها گسترش چشمگیری یافت و با استفاده از پر کنندههای ارزان قیمت نظیر کائولن، در مصرف رزینهای گران قیمت صرفهجویی شد.
کائولن بعنوان بسط دهنده ارزان قیمت در صنعت ساخت( PVC پلی وینیک کلراید) نیز مصرف میگردد. کائولن همچنین در ساخت نایلون، پلیاستر و سایر پلاستیکها، تهیه رنگینهها (بجای رنگی اکسید تیتانیوم) نیز مورد استفاده قرار میگیرد.
- کائولن معدن کاوان در کاربرد شیمیایی:
کائولن دارای آلومینا و سیلیکا است (افزودنی سیمان، تولید زئولیت و سولفات آلومینیوم، تولید فایبرگلاس، کاتالیزور و عمل کنندههای کاتالیزور، ظروف دارویی، حشرهکشها، غذای حیوانات).
یکی از پرارزشترین مصارف کائولن، مصرف در صنایع شیمیایی و بویژه بعنوان کاتالیزور میباشد. در ایالات متحده امریکا حدود ۵ درصد کل مصرف کائولن در این زمینه صورت میپذیرد. خصوصیات کائولن مصرفی محدود به شرکتهایی میشود که از تکنولوژی خاص و پیشرفته برخوردار هستند و از مصارف عمده کائولن، استفاده بعنوان کاتالیزوز FCC در صنایع نفت و ساخت زئولیت مصنوعی است. ترکیبات آلومینیوم از جمله سولفات آلومینیوم که در صنعت کاغذ سازی و در تصفیه آب مصرف عمده دارند، از دیگر مصارف عمده کائولن در این بخش میباشد.
اصولاً مصرف کائولن در کاتالیستها در ایالات متحده امریکا،کشورهای اروپای غربی و برخی از کشورهای آسیایی از قبیل ژاپن، کره جنوبی صورت میگیرد. میزان مصرف کائولن در کاتالیستها در سال ۱۹۹۷ توسط ایالات متحده امریکا بالغ بر ۲۲۷ هزار تن بوده است که در سال ۱۹۹۸ با کمی کاهش به ۲۰۰ هزار تن رسیده است.
۹.کائولن معدن کاوان در داروسازی :
کائولن در صنعت داروسازی با ترکیب سیلیکات آلومینیوم آبدار شناخته شده است. این کانی در تهیه داروهای ضداسهال کاربرد دارد که این داروها هر ۴ ساعت یک بار و به مقدار ۲ تا ۶ گرم مصرف می شود. از کائولن برای تهیه پمادهای مسکن درد، کاهش دردهای التهابی و معالجه بیماری های معده و روده استفاده می شود.
داروهای مرکب از کائولن عبارتست از : شربت کائولن پکتن، شربت کائولن کودکان، شربت کائولن و مرفین، شربت کائولن و پماد کائولن می باشد.داروهای حاوی کائولن ممکن است عوارض جانبی از قبیل : حساسیت مفرط با علائم سقوط فشار خون، کهیر، تب، درد مفاصل، تاول های سرخک مانند، ناراحتی های گوارشی، تهوع، سردرد داشته باشد و با قطع دارو از بین برود.
- کائولن معدن کاوان در مصالح ساختمانی :
کائولن در ساخت انواع مصالح ساختمانی بکار میرود. در برخی از این مصالح بعنوان ماده اصلی و در برخی بعنوان ماده کم اهمیتتر صرف میگردد. عموماًدر این صنایع از کائولن نامرغوب استفاده میشود. از موارد مصرف کائولن در ساختمان سازی میتوان از ساخت آجر، آجرنما، اتصالات لوله ساخته شده (از انواع رسها) کاشی کف و دیواری، محصولات بهداشتی، پوشش سقف و استفاده در نمای ساختمانها نام برد. همچنین از کائولن در ساخت بعضی از آسفالتها و موزائیک سقفی و نوعی کف پوش بنام لینولیوم، ساخت سیمان های سفید استفاده میگردد ولیکن در ساخت سیمان معمولی کاربردی ندارد.
کائولن بعنوان پر کننده و افزایش دهنده مقاومت مکانیکی در صنایع فیبر شیشه، پشم سنگ و سایر تولیدات عایق کننده بکار میرود. حجم کمی از کائولن نیز بعنوان پر کننده و تقویت کننده در صنایع دیوارهای پیش ساخته گچی و سایر تولیدات پیش یاخته بکار میرود.
استانداردها:
بهترین کائولنها ۲۰ درصدناخالصی دارند. از این رو باید کائولن را تغلیظ کرد و مواد قلیائیK۲O,Na۲O,CaO آن را به کمتر از ۵/۱ درصد رسانید .وجود عدسی های آهندار و سنگهای ولکانیک آندزیتی تا بازالتی و فلدسپات های دگرسان نشده باعث پائین آمدن کیفیت کائولن میشود. سولفات کلسیم (گچ) نقطه ذوب کائولن را پائین میآورد.
حداکثر انقباض کائولن ۱۲ درصد است و برای بالا بردن آن میتوان به آن مونت موریونیت افزود. کائولن مصرفی در کاشیسازی، در روند گامههای گوناگون شکل دادن و گرم کردن، شکلپذری و تحمل حرارت، نباید با از دست دادن آب نقصان حجم پیدا کند،در غیر اینصورت برای این گونه صنایع کار آمد نیست. این پدیده که بعنوان چروک خوردن همراه با ایجاد ترک (Sherinkage) نام دارد، در صنایع کاشیسازی از اهمیتی ویژه برخوردار است.
کائولن مصرفی در صنعت باید دارای مشخصات عمومی زیر باشد :
۱- درصد آلومین آن بایستی از ۳۰ درصد به بالا باشد تا مرغوبیت پیدا کند.
۲- میزان اکسیدهای آهن نباید از ۱ درصد بیشتر باشد.
۳- میزان اکسید تیتانیوم باید به ۲/۰ درصد کاهش یابد.
۴- جمع اکسیدهای قلیایی نباید از ۲ درصد فراتر باشد.
۵- حداکثر میزان CaO، ۲/۰ درصد و MgO، ۳/۰ درصد باشد.
۶- افزایش میزان کائولینیت نسبت به سایر کانیهای موجود باعث مرغوبیت کائولن میشود. بطور معمول درصد این ماده خاکی باید از ۷۰ درصد بیشتر باشد.
۷- دیرگذاری کائولن باید در حدود ۱۷۰۰ درجه سانتیگراد باشد.
۸- مدل گسیختگی(Modulus of Rupture) آن می بایست بیش از Kg/m۲۱۰ باشد.
اگر کائولن آنقدر گرما بپذیرد تا پیوندش بشکند، ۳O۲Al،SiO۲ بدست خواهد آمد که به آن مولیت و شاموت گویند (فرآوردهای که در تولید آجر نسوز بکار میرود).
نقطه گداز بالا،ظرفیت کم آب و پایداری در برابر دمای بالا سبب میشود تا کائولن مادهای مهم در بین خاک های رس نسوز بشمار آید. کائولن در صنایع چینی و سرامیکسازی به کنترل خواص شکلپذیری ماده خام کمک میکند و استحکام فرآورده را در برابر دما و گرما و خشکی بالا میبرد و به صیقلپذیری سطح پوشیده شده کمک میکند.کائولن مطلوب برای پوشش کاغذ باید سفید باشد و در آب به سرعت معلق شود. درجه غلظت پائین داشته باشد و دارای دانهبندی ریزی باشد. مقدار کوارتز کائولن باید کم باشد تا فرسایش ماشینآلات را کاهش دهد. کائولن شسته شده مرغوب بیشتر خواص بالا را دارد. یک راه ارزشیابی کائولن مرغوب در پوشش کاغذ، شفافیت آن است.
کائولن در لاستیکسازی وقتی به اندازه کمتر از ۱۸ درصد حجم بکار گرفته شود قدرت کشش لاستیک را بالا میبرد و درجه از هم پاشیدن آن را کم میکند. کیفیت مطلوب در کائولن مورد مصرف در صنعت سرامیک، درخشندگی خوب بعد از پخته شدن، مقاومت و شکلپذیری و درجه غلظت است.
رنگ سفید،خاصیت پوشش خوب، نرم بودن، نداشتن ویژگی سایندگی، ضریب هدایت حرارتی و الکتریکی پایین و قیمت به نسبت ارزان محسنات کائولن است.
کائولن معدن کاوان در صنعت کاغذ:
۵۰ % کائولن در صنعت کاغذ سازی استفاده می شود که در آن کائولن به اندازه ریز (۹۰% ذرات کوچکتر از ۲ میکرومتر) و درشت (۵۰% کوچکتر از ۲ میکرومتر) تقسیم شده و میبایست رسهای با ویسکوزیته کم مورد استفاده قرار گیرند. در صنعت کاغذ سازی کائولن به عنوان ماده پرکننده و روکش استفاده می شود. درخشندگی بر اساس استاندارد متغیر است، محتوی باکتری و قارچ محلول آن میبایست به دقت کنترل شود.
کائولن معدن کاوان با کاربری در پوشانندهها:
کائولینیت ۱۰۰-۹۰%، Fe۲O۳ کم (۸/۱-۵/۰%)، تقریبا بدون کوارتز ساینده، درخشندگی ۸۵%، اندازه ذرات ۸۰ تا ۱۰۰% آنها کمتر از ۲ میکرومتر، ویسکوزیته بروکفیلد کمتر از cpe 7000، خواص رئولوژیکی نقش مهمی دارند، میبایست توانایی پخش در آب و تشکیل یک مایع آبکی با ویسکوزیته کم را داشته باشد.
کائولن معدن کاوان با کاربری درسرامیک:
۸۵-۷۵% کائولینیت تولید شده در صنایع سرامیک به مصرف می رسد، چراکه دیگر کانیها در رنگ، ویسکوزیته و سایندگی تاثیر میگذارند. کائولن مورد استفاده در چینی استخوانی میبایست درخشندگی ۹۱-۸۳% در دمای 1180C و کمتر از۹/۰% Fe۲O۳ داشته باشد. اندازه دانه در مقاومت و سختی موثر است، لذا انواع ریزتر برای چینی استخوانی، حدواسط برای ظروف سفالی و انواع درشت برای سرویس بهداشتی کاربرد دارد.
کائولن معدن کاوان باکاربری نسوز:
انواع نسوز کائولینیت باید تا دمای ۱۵۰۰ C صلابت خود را حفظ کند، برپایه مناسب بودن و درجه آن به ۴ دسته تقسیم میشوند. آزمایشات مختلفی برای سنجش درجه نسوزی و مقاومت دربرابر حرارت، فرسایش و تخلخل آن انجام میشود. رسهای مورد استفاده در نسوز ممکن است براساس مقدار Al۲O۳تقسیمبندی شوند که نوع کم آهن و کمآلکالی ارجحیت دارد.
کائولن معدن کاوان درفایبرگلاس:
به عنوان منشاء Al۲O۳ و SiO۲ شناخته میشود، در حالت معمول Al۲O۳ و SiO۲ با حداکثر یک درصد Fe۲O۳، دو درصد Na۲O و ۱% آب.
مواد آرایشی:
حداکثر ۲ ppm آرسنیک، ۲۰ ppm فلزات سنگین، ۲۵۰ ppm کلریدها، ۱۵% وزنی نقصان در اثرحرارت دادن،
PH 5/0 ± ۵/۷.
کائولن معدن کاوان در بازیافت:
بازیافت روزافزون کاغذ بیش از هرچیز در بازار خمیره کاغذ موثر است تا در بازار انواع کانیهای پرکننده یا پوشاننده. بعلاوه بیشتر کاغذ بازیافت شده در چاپ روزنامه مصرف شده که هرچند کم به کائولن نیازمند است.
بعد از بازیافت کاغذ، هرکانی پرکننده آن یا رنگدانه پوششی به صورت یک مایع مخلوط جداشده که درحال حاضر دفع میشود. بنابراین در حال حاضر چنین کاغذی وقتی بازیافت میشود برای کاربردهای مجدد به کائولن تازه محتاج است. فایبرگلاس به مقدار کمی بازیافت میشود. سفالهای شکسته در موارد محدودی مصرف میشوند و نسوزها برای چند مرتبه بازیافت میشوند که در استفاده مجدد، ساخت نسوزهای رسی در نظر نیست.
جایگزینی های کائولن در صنایع مختلف:
کائولن دارای خواصی چون دارا بودن خاصیت پوششی بسیار خوب، داشتن رنگ سفید، ثابت بودن خواص فیزیکی با تغییرات PH، کم بودن قابلیت هدایت گرمایی و الکتریکی، نرم بودن و ساینده بودن و ارزانی قیمت میباشد. این ویژگی ها باعث شده است که از نظر کانی و یا ترکیبات جایگزینی برای این ماده معدنی در صنعت دچار محدودیت شویم.
جایگزینی ترکیبات دیگر به جای کائولن نیاز به مطالعات وسیعی در زمینههای خواص کاربردی و شاخصهای اقتصادی دارد. این مطالعات باید به صورت موردی در بخشهای مختلف صنعت صورت پذیرد.
جایگزینی کائولن در رنگ سازی
کائولن اصولاً بعنوان یک رنگدانه،با رنگ سفید که به طور جزئی جایگزین دیاکسید تیتانیم میشود، در رنگها بکار میرود. کائولن همچنین پایداری رنگها را افزایش میدهد زیرا ذرات پهن کائولن تمایل به همپوشانی دارند و بدین ترتیب پوسته رنگ تقویت میشود. در این نقش کائولن با میکا، تالک و دیگر کانیهای سیلیکاتی رقابت میکند.
جایگزینی کائولن در ماده ضد بلوکهشدن:
دیاتومیت، سیلیستهنشستی، تالک.
جایگزینی کائولن در جذبکننده، حمل کننده:
آتاپولگیت، بنتونیت، دیاتومیت، پیت، پومیس، پیروفیلیت، سپیولیت، تالک، ورمیکولیت، زئولیت.
جایگزینی کائولن در سرامیک:
فایبرگلاس، مشابههای پلاستیکی.
جایگزینی کائولن در پرکننده و پوشش دهنده
کائولن عموماًبعنوان بهترین کانی پرکننده و پوشش دهنده در دسترس برای کاغذ شناخته شده و در آینده نیز چنین پیشبینی میشود.کربنات کلسیم در صنعت کاغذسازی رقیب کائولن بوده و کانیهای گروه تالک نیز اگر مشخصات فنی لازم را داشته باشند، ممکن است جانشین کائولن گردند.
جایگزینی کائولن در تولید سموم دفع آفات
کائولن به عنوان یک حامل و پر کننده معدنی برای سم به کار گرفته میشود. به جز کائولن مناسبترین پرکنندگان معدنی که بعنوان حامل و رقیق کننده استفاده میشوند عبارتند از دولومیت، فولرزارت، تالک، ژیپس، آهک،پرلیت و پیروفیلیت.
جایگزینی کائولن در ریختهگری:
بوکسیت و آلومینا، کرومیت، الیوین، پرلیت، پیروفیلیت، ماسهسلیسی، ورمیکولیت، زیرکن.
جایگزینی کائولن در نسوز:
آندالوزیت، بوکسیت، کرومیت، کیانیت، دولومیت، گرافیت، منیزیت، الیوین، پیروفیلیت، سیلیس، سیلیمانیت، زیرکن.
جایگزینی کائولن در اصلاح خاک:
بنتونیت، دیاتومیت، ژیپس، پرلیت، ورمیکولیت، زئولیت.
جایگزینی کائولن در پلاستیک:
در پلاستیک ها کاربرد اصلی کائولن در پر کردن PVC، نایلون ها و پلیاسترهاست که رقبای عمدهاش کربنات کلسیم و کانی های سیلیکاتی هستند.
جایگزینی کائولن در کاغذ:
از نظر مصرف کائولن، رتبه اول را کاغذسازی و بعد از آن سرامیک سازی، صنعت دیرگدازها و لاستیکسازی رتبههای دوم تا چهارم را در جهان به خود اختصاص داده اند.
بزرگترین صنعت مصرف کننده کائولن در این سال، صنعت کاغذسازی بوده است بطوری که ۴۵ درصد کائولن مصرفی، در این صنعت مورد استفاده قرار گرفته است. اصولاً بزرگترین مناطق تولید کننده کاغذ در جهان، عمدهترین مصرف کننده کائولن در جهان هستند (مناطق امریکای شمالی و اروپای غربی) در آسیا از دیرباز در صنایع سرامیکسازی مصرف شده است و این در حالیست که مصرف این کانه در صنعت کاغذسازی در این قاره با افزایش کارخانههای سازنده انواع کاغذ و تغییرات در تکنولوژی ساخت در حال افزایش میباشد.
صنعت کاغذسازی، بزرگترین مصرف کننده این کانه در ایالات متحده آمریکا، ژاپن و آلمان بوده است، در حالیکه در کره جنوبی و تایوان صنعت سرامیک سازی، بعنوان بازار اصلی مصرف این کانه اعلام گردیده است.
جایگزینی کائولن در صنایع پلاستیک
کائولن جانشین پلیمرهای گران قیمت شده و موجب ارزانی محصول گردیده است. مصرف نهائی در این صنعت طی سال ۱۹۹۹ معادل ۵/۰ درصد مصرف جهانی و برابر با ۱۳۵ هزار تن بوده است.
بعد از صنعت کاغذسازی و مصارف کاربردی کائولن بعنوان پرکننده، بزرگترین مصرف کننده کائولن صنایه ساختمانی میباشند. ۱۲ درصد کائولن مصرفی در سال ۱۹۹۹ بعنوان ماده اصلی دریک طیف گسترده صنایع ساختمانی بکار رفته است.
این طیف شامل صنایع آجر،سیمان،فایبرگلاس، پوششهای سقف و دیوارهای گچی میباشد.
بسیارعالی و کامل